Mechanics for Modelling
The research area Mechanics for Modelling focuses on analytical, numerical and experimental methods for the mechanical modelling of materials, systems and processes. The focus is on mechanical aspects of the industrial digitalisation. The synergy between realistic experiments, non-linear simulations and data-based methods is systematically used to describe, analyse and optimise complex mechanical behaviour.
The expertise of the research group currently includes mechanical characterization and modeling of metals and polymers, nonlinear structural analysis using FEM and thermo-mechanical process simulation for additive manufacturing, and experimental dynamics for characterization and analysis of dynamic systems. By 2025, competencies in the area of data-based methods (design of experiment, response surface modeling, neural networks, etc.) will be developed.
Material modelling for FEM
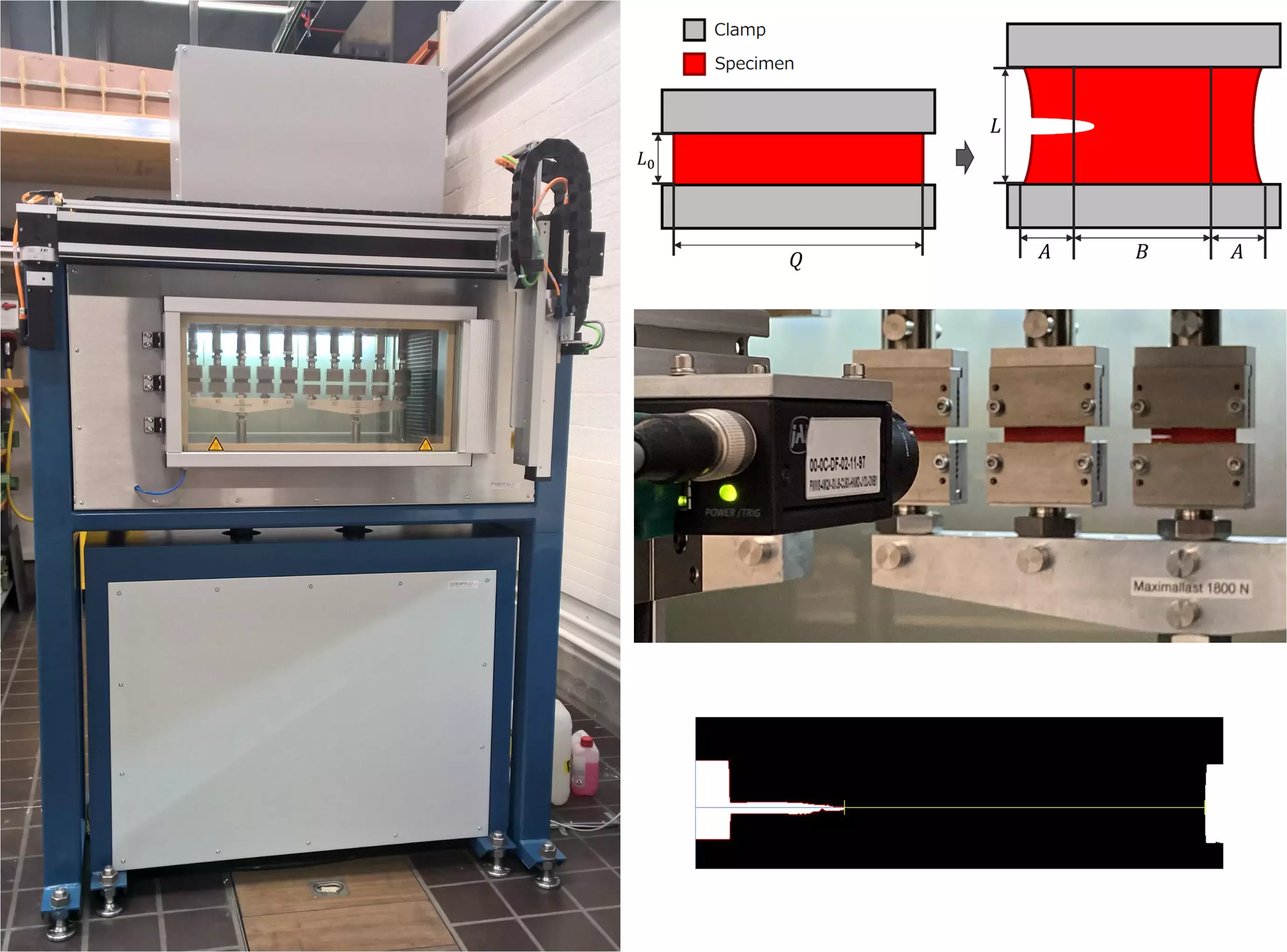
The detailed analysis and reliable design of thermo-mechanically highly loaded structures requires a physically well-founded description of the underlying material behaviour. Material models are primarily used in analysis and design by means of nonlinear finite element methods (FEM). Examples range from steam turbines, sealing and damping elements to additively manufactured, metallic components. Particularly in the context of the energy transition, consistent lightweight construction and the realisation of a circular economy, the characterisation and description of the mechanical behaviour of new materials is of special importance.
Our expertise includes the mechanical, thermo-mechanical and thermo-physical characterisation and modelling of polymers and metals. The material models used describe linear and non-linear elasticity, viscoelasticity, plasticity and viscoplasticity as well as fatigue (LCF, HCF) and creep damage for lifetime prediction. Temperature and rate dependencies are also taken into account. Thermo-physical parameters include density, thermal conduction as well as thermal expansion.
Project example: Measurement, Calibration & Modeling of High Performance Polymers
Process simulation for additive manufacturing
Additive manufacturing of metallic components enables the production of complex and highly integrated lightweight and functional parts. At the same time, it has great potential to disrupt the existing manufacturing landscape with its high degree of flexibility and sustainability. However, the great complexity of this promising manufacturing technology requires a great deal of know-how in order to realise the necessary reliability and economic efficiency.
Thermo-mechanical process simulation supports the design and manufacturing preparation of additively manufactured components to improve the reliability and economic efficiency of this promising process. Our expertise lies in the simulation of process-induced thermo-mechanical distortion or residual stresses. For this purpose, both simplified inherent strain and advanced thermo-mechanical approaches are applied. To ensure reliable predictions, we perform a comprehensive thermo-physical characterization of additively processed materials. We further specialize in component-like calibration of all leading process simulation solutions. On our Aconity3D MIDI facility, which we operate in collaboration with the ZHAW IMPE, we develop dedicated in-situ experiments for advanced calibration of laser absorption or thermal conductivity of powders. In this way, we ensure reliable predictions of temperatures, stresses and distortions. On this basis, build-up strategies, support structures and additively manufactured components can be optimized and distortion compensated for prior to manufacturing.
Experimental dynamics
Another focus is on the development and research of novel measurement methods for the experimental characterization of dynamic systems and their application to solve challenging problems in practice.
We apply our expertise in the area of vibration of and wave propagation in mechanical structures to develop digital models (digital twins), focusing on a comprehensive approach with strong synergies between theory, experiment and simulation. With our competences we cover experimental mechanics holistically. This includes the conceptual design of the measuring equipment, selection of sensors, data acquisition, planning of experimental camapaigns and especially the analysis and processing of large data sets using numerical and statistical methods.
Applications range from classical machine dynamics (multi-body dynamics and modal analysis), to the development and optimization of dynamic systems, to research on sensor technology and measurement methods based on dynamic principles. In addition, we have competences in the analysis of vibrations of rotating systems (rotor dynamics) and their coupling with fluids, as they occur for example in water turbines or as they are used in fluid sensors.
Experimental Infrastructure & Processes
- Measurement, calibration & modeling of high performance polymers
- Measurement of thermal expansion coefficients using dilatometry(PDF 352,6 KB)
- Measurement of heat conduction using Laser Flash Analyzer(PDF 339,7 KB)
- In-situ experiments in the PBF-LB/M process at the ZHAW IMES / IMPE research facility Aconity3D MIDI (Flyer on request)
- Vibration Measurement and Scanning Laser Doppler Vibrometer Polytec PSV-400 (Flyer on request)
Projects
We conduct research in the field of mechanics and have already successfully completed numerous projects. You can find a selection of these projects here
-
Reduced Residual Stresses through Support Structure Optimization in Laser Powder Bed Fusion
Metal additive manufacturing (AM) has proven to be an attractive and viabletechnology for industry to produce complex components and/or small lot sizes. Thereliability and thus acceptance of metal laser powder bed fusion (LPBF) remains achallenge though. Severe thermal gradients can occur causing excessive ...
-
Digital twin of ROSTA rubber spring elements
Digital twins are derived from high-fidelity simulations to efficiently predict the non-linear characteristics of ROSTA rubber spring and damper systems. In the context of digitalisation, customer needs are thus better satisfied and own development processes become more efficient.
-
Optimisation of the tooth root geometry of plastic gears
The use of plastic gears in drives is growing rapidly, especially in the module size range 0.5 to 1.5 mm and at maximum load cycles during the product life of 105 to 106. A key factor for reliability is the tooth root strength of the gears. Although injection moulding, which is the common production method for ...
-
Mechanobiological plastic model
Plastics are experiencing increased interest in medical technology. Due to their mechanical properties, plastics correspond more closely to human tissue than metallic materials such as titanium or cobalt-chromium. The so-called mechanobiology of human soft tissue, especially cartilage and intervertebral discs, is ...
-
Machine Learning Enhanced Process Simulation in Laser Powder Bed Fusion (LPBF)
The project aims to develop and implement dedicated calibration procedures and parts that are tailored to critical applications of ABB and Sauber, to improve the accuracy of distortion predictions for specific components. Machine learning is then used to enhance simulations also beyond the calibrated regime. This ...
More Projects
Publications
-
Brenner, Lorenz; Jenni, Christian; Guyer, Flurin; Stähli, Patrick; Eberlein, Robert, Huber, Matthias; Zahnd, André; Schneider, Martin Albert; Tillenkamp, Frank,
2021.
Journal of Loss Prevention in the Process Industries.
75, S. 104706.
Verfügbar unter: https://doi.org/10.1016/j.jlp.2021.104706
-
Mayer, Thomas; Brändle, Gabriel; Schönenberger, Andreas; Eberlein, Robert,
2020.
Simulation and validation of residual deformations in additive manufacturing of metal parts.
Heliyon.
6(5), S. e03987.
Verfügbar unter: https://doi.org/10.1016/j.heliyon.2020.e03987
-
Eberlein, Robert, Pasieka, Lucian,
2020.
Prediction of long-term behavior for dynamically loaded TPU.
Advanced Materials Letters.
11(1), S. 1-6.
Verfügbar unter: https://doi.org/10.5185/amlett.2020.011458
-
Eberlein, Robert; Pasieka, Lucian; Rizos, Dimosthenis,
2019.
Validation of advanced constitutive models for accurate FE modeling of TPU.
Advanced Materials Letters.
10(12), S. 893-898.
Verfügbar unter: https://doi.org/10.5185/amlett.2019.0031
-
Eberlein, Robert; Fukada, Yuta; Pasieka, Lucian,
2020.
Fatigue life analysis of solid elastomer-like polyurethanes
.
In:
Fatigue Crack Growth in Rubber Materials.
Berlin, Heidelberg:
Springer.
S. 179-202.
Advances in Polymer Science.
Verfügbar unter: https://doi.org/10.1007/12_2020_68
-