Low-cost prosthetic hands for children from a 3D printer
Conventional prosthetic hands are very expensive. This is why ZHAW students have developed prosthesis modules that could be affordable even for children in developing countries. They work without any high tech and their parts are made with a 3D printer.
For people in developing countries, conventional prostheses are simply unaffordable. Expensive high-tech solutions are controlled through muscle activity and are therefore able to perform all kinds of gripping functions, and they also look similar to a real hand. But even in Switzerland, such high-tech prostheses are not necessarily the best solution for children: they are heavy and when children are playing, they can be more of a hindrance than a help. Another problem is that children quickly outgrow their prostheses. ZHAW students have therefore developed low-cost prosthetic modules for everyday use and sports which work without high tech and are made with a 3D printer.
Modular system with exchangeable parts
Customisable, light yet sturdy and low cost – these were the requirements for children’s prosthetic hands that drove Systems Engineering students at the ZHAW School of Engineering when they started brainstorming. Their best ideas have led to a patented modular system for children’s prosthetic hands. “It became clear early on that a universal prosthesis for all potential activities wasn’t compatible with the specified requirements”, says ZHAW researcher Wilfried Elspass. In contrast, the modular system that has been developed allows different parts - depending on the activity - to be attached to a specially developed prosthetic shaft. Besides a universal everyday prosthesis, there are already prostheses for cycling, tennis, and downhill and cross-country skiing.
Made in a 3D printer
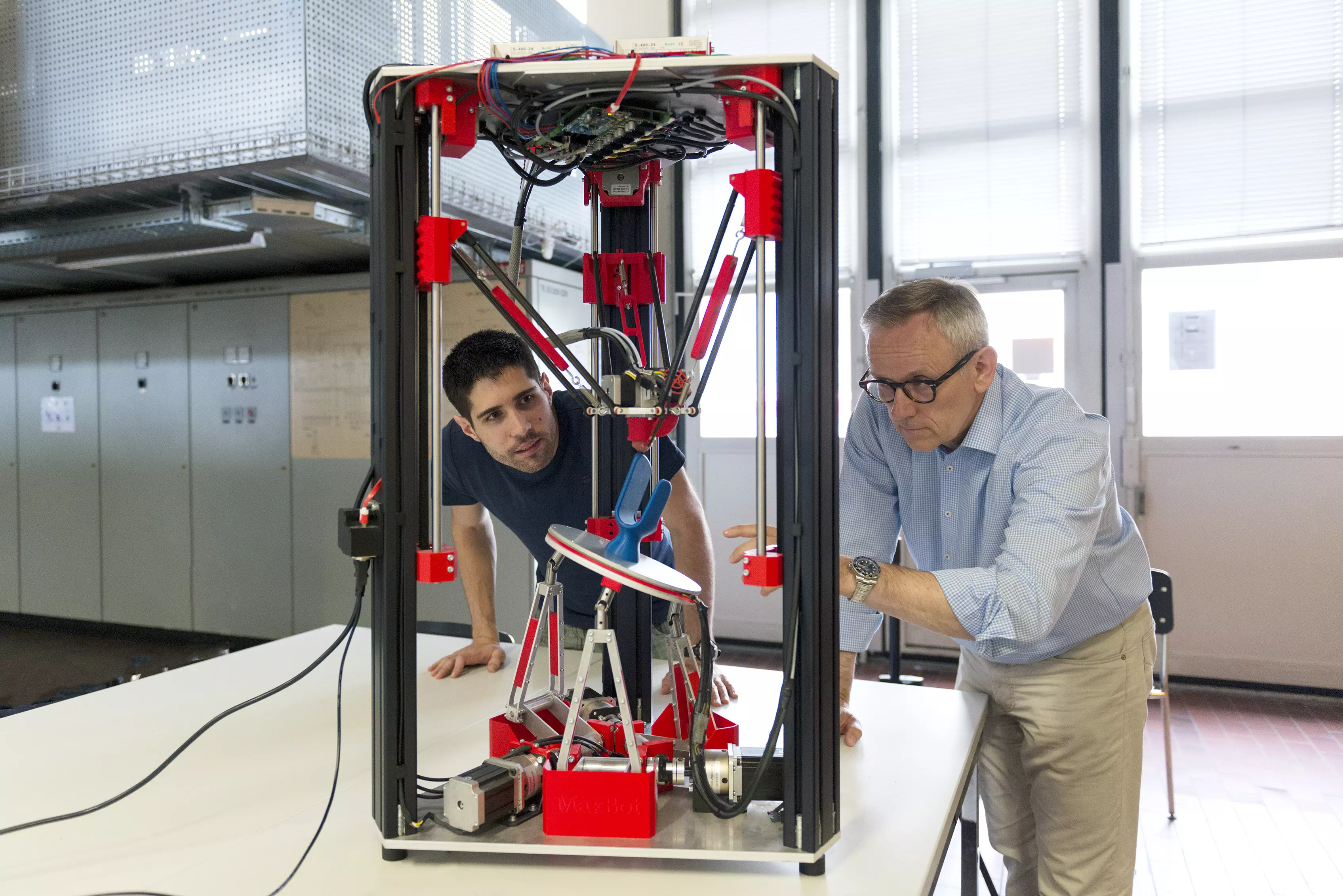
The prosthesis system developed at the ZHAW School of Engineering is designed in such a way that children can handle it without difficulty. The individual modules weigh only about 150 grams. The prostheses for cycling and skiing are purely mechanical, while the everyday and the tennis prostheses have a simple, integrated sensor system. The plastic parts are made with a 3D printer. “Production with 3D printing isn’t just very low-cost, it also has the great advantage that prostheses can be customised for the individual user”, says Fabian Schollenberger, who has continued to work on developing the prostheses for his Master’s thesis. The plastic used for the prostheses is light yet sturdy. While it is considerably less stiff and strong than aluminium, this potential shortcoming can largely be compensated for through the design and construction.
Foundation for low-cost prostheses
Zurich doctor Andreas Trojan, who initiated the development of low-cost prostheses, wants to continue driving it forward through the Appsocial foundation, established especially for this purpose. “The goal is that children can wear a prosthesis while playing without being afraid of breaking anything”, says Andreas Trojan. “Our prostheses are to be regarded as functional tools.” The prototypes have performed well in initial tests. The test person used the prostheses intuitively without any previous training.
Downloads
- Image: multiple prostheses
- Image: everyday prosthesis
- Image: tennis prosthesis
- Image: skiing prosthesis
- Image: cycling prosthesis
- Image: 3D printer
- Image: scanner
- PDF: media release (in German)(PDF 128,5 KB)
Higher-resolution images are available upon request.
Contacts
Prof. Wilfried J. Elspass, head of the Systems Engineering research area, Institute of Mechatronic Systems, ZHAW School of Engineering, phone: 058 934 78 28, e-mail: wilfried.elspass@zhaw.ch
Matthias Kleefoot, Public Relations, ZHAW School of Engineering, phone: 058 934 70 85, e-mail medien.engineering@zhaw.ch