Kanban
Wir sind umgezogen!
Sie finden diesen Beitrag neu unter https://www.leanhealth.ch/transformation/what/
Eva Hollenstein, Alfred Angerer (V01)
Zusammenfassung
Bei Kanban handelt es sich um eine in Japan entwickelte Methode zur Steuerung des Materialflusses. Traditionell kommt Kanban zur bedarfsorientierten Bereitstellung von Material bzw. Ressourcen zum Einsatz. Dadurch werden lange Wartezeiten und zu hohe Lagerbestände vermieden. Die Prozessstufen sind bei der Methode so miteinander verbunden, dass die einzelnen Einheiten erst dann zur Verfügung gestellt werden, wenn eine Materialentnahme stattfand und der Bestand unter das Mindestniveau gesunken ist. Heutzutage wird Kanban zunehmend bei vielen internen Materialflüssen im Gesundheitswesen eingesetzt.
Zielsetzung / Leitfragen für die Praxis
Kanban wurde in Japan von der Toyota Motor Corporation zur Produktivitätssteigerung des Unternehmens entwickelt (Dickmann, 2009). Die Kanban-Methode, auch Pull-Prinzip genannt, wird zur bedarfsorientierten Steuerung der Wertschöpfungskette verwendet. Ziel ist es, die Prozesse entlang der Wertschöpfungskette zu optimieren und somit einen bestandsminimalen Materialfluss zu erreichen.
Das Kanban-System bietet Hilfestellung bei folgenden Fragen im Spital:
- Wann soll die Materialbereitstellung an einer bestimmten Spitalstation erfolgen, um eine reibungslose und kosteneffiziente Patientenbehandlung sicherzustellen?
- Wie hoch soll dabei die optimale Bestellmenge sein?
- Wie können Bestellvorgänge prozessorientiert in den Spitalalltag integriert werden?
Voraussetzungen / Notwendige Ressourcen
Für eine erfolgreiche Einführung der Methode muss das Unternehmen bzw. die Organisation einige Voraussetzungen erfüllen. Kanban benötigt einen gerichteten und relativ konstanten Materialfluss. Das Material muss einheitlich und gut definierbar sein. Das System eignet sich sehr gut für einfache oder komplexe, aber genau definierbare Materialien. Grundsätzlich kann das System dort eingesetzt werden, wo es sich um eine standardisierte Leistungserstellung handelt (Lean Magazin, 2015). Nicht geeignet ist das Kanban-System für Materialien mit stark schwankendem Bedarf.
Detailbeschreibung des Tools
Kanban folgt einer Pull-Logik. Beim Pull-Prinzip handelt es sich um das bedarfsorientierte „Nachziehen“ der benötigten Materialien. Nachfolgende Abbildung 1 zeigt die grundlegenden Unterschiede im Vorgehen beim Push-Prinzip und beim Pull-Prinzip.
Nachdem der Verbraucher das benötigte Material entnommen hat, gibt dieser ein Signal in Form einer Karte (jap. Kanban = Karte), die benötigte Menge erneut zu produzieren bzw. nachzuliefern (Dickmann, 2009). Die Karten dienen als Auftragsdokument und enthalten alle notwendigen Informationen. Das System basiert somit auf dem tatsächlichen (Material-) Verbrauch und dient der Organisation zur Just-in-time-Produktion. Ein Kanban ersetzt die herkömmliche Auftragssteuerung durch eine Verbrauchssteuerung, indem aus zwei hintereinander liegenden Prozessen ein verknüpfter, selbststeuernder Regelkreis gebildet wird.
Kanban hat zwei Funktionen: Die erste Funktion ist ein Indikator zur Her- und Nachbestellung des Materials auf vorgelagerter Produktionsstufe. Sollte das Material in einer Produktionsstufe verbraucht sein, dient Kanban als Bestellkarte, mit der die vorgelagerte Produktionsstufe zur erneuten Herstellung dieses Materials veranlasst wird (Lean Magazin, 2013). Ausserdem dient Kanban für das neu produzierte Material als Identifikationskarte, die alle notwendigen Informationen enthält (Gabler Wirtschaftslexikon, o.J.).
Das Vorgehen bei Implementierung des Kanban-Systems lässt sich wie folgt gliedern:
- Identifikation der Materialien, die mit dem Kanban-System bestellt werden sollen.
- Definition aller Informationen für die Kanban-Karte: Produktinformation, Barcode, Lagerplatz, an dem das Material abgeholt werden soll.
- Definition der Mindestmenge, bei der die Bestellung erfolgen soll.
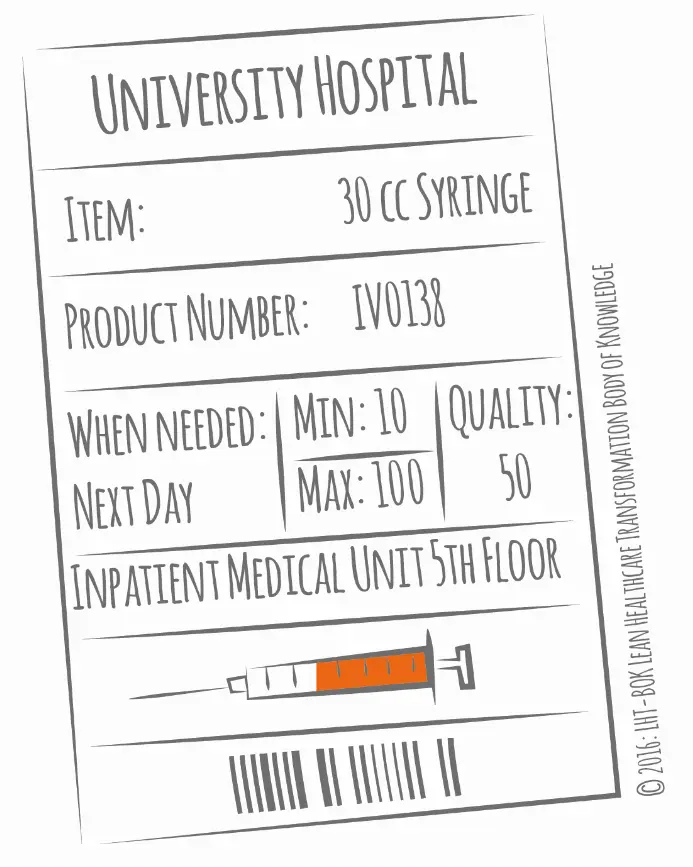
Beispielsweise kann das Kanban-System zur Versorgung des OP-Raums mit notwendigem Medizinmaterial verwendet werden. Jedes Materialverbrauchsstück wird dabei in einer separaten Box platziert. Diese Box enthält auch eine Informationskarte mit allen notwendigen Angaben für die Nachbestellung, inklusive der Menge, Barcode, Produktbild und Produktbeschreibung (siehe Abbildung 2). Die Karte sollte bereits dann gezogen werden, wenn der minimale Materialbestand erreicht ist. Das bedeutet, dass zwar noch genügend Material vorhanden ist, aber die Bestellung erfolgen sollte, um einen reibungslosen Ablauf zu gewährleisten. Das notwendige Material wird anhand dieser Informationen besorgt und in der Box platziert.
Das Seattle Children’s Hospital verwendet ein sogenanntes „two-bin demand-flow“-Kanban-System. Dabei werden rund 95 Prozent des benötigen Materials in Behältern zugestellt. Gegenstände, die zu gross für den Behälter sind, werden über Kanban-Karten angefordert. In den meisten Arbeitsbereichen beinhalten die Behälter genau den Materialbedarf, der pro Woche anfällt. Sobald der leere Behälter vom Verbraucher in einem ausgewiesenen Bereich platziert wird, wird eine Wiederauffüllung veranlasst. Der Materialdienst holt die leeren Behälter ab und bringt sie in das zentrale Warenlager. Dort werden sie gescannt, was dem primären Vertriebspartner signalisiert, dass die Vorräte aufgefüllt werden. Innerhalb von 24 Stunden wird der aufgefüllte Behälter wieder an die anfordernde Stelle retourniert (Wellman, Hagan & Jeffries, 2011).
Im Seattle Children‘s Hospital hat der Einsatz des Systems zu beachtlichen Ergebnissen geführt (siehe Tabelle 1):
In diesem Video wird der Einsatz des „Two-bin-demand-flow“ anschaulich erklärt.
Stärken und Schwächen
Herausforderungen
Das Kanban-System stellt einen konträren Ansatz zu den Abläufen dar, die häufig im Spital vorgefunden werden. Aus diesem Grund muss die Einführung des Systems mit den entsprechenden Change-Management-Massnahmen begleitet und ein gewisses Problemverständnis geschaffen werden.
Fehlt während der Arbeit ein bestimmter wichtiger Gegenstand, ist häufig die natürliche Reaktion das nachträgliche Bestellen überdimensionierter Mengen, um nicht noch einmal in die gleiche Situation zu geraten. Kanban verhindert diese Reaktion, indem jede Fehlmenge auf ihre Ursache hin geprüft wird (vgl. Root-Cause-Analyse und 5S) und nachvollzogen wird, ob es sich um eine einmalige Schwankung handelte oder ob es regelmässig zu Engpässen bzw. Fehlmengen dieses Gegenstands kommt.
Anstatt dem Problem einfach mit grösseren Bestellmengen zu begegnen, muss sich der Kanban-Verantwortliche demzufolge fragen, ob und wie der Meldebestand angepasst werden muss (Graban, 2012).
Stärken
Grosses Potential liegt bei Kanban insbesondere in der Reduzierung von Lagerbeständen, somit auch bei der Kapitalbindung und des Umlaufvermögens (Lean Magazin, 2015). Dies erfolgt ohne Verzicht auf die hohe Lieferbereitschaft und ohne zusätzliche Bestell- und Transportkosten. Steuerungsaufwand wird durch den Einsatz des Kanban-Systems erheblich reduziert, somit wird das Spitalpersonal entlastet. Das System ist einfach in der Ausführung, effizient und visuell gut nachvollziehbar. Die Ausrichtung auf den Verbraucher und seinen Bedarf ist ein grosser Vorteil des Prinzips, da nur so viel, wie tatsächlich benötigt, verwendet wird. Dadurch wird eine Bedarfsabdeckung erreicht und die Prozesse werden kosteneffizient gestaltet.
Schwächen
Das System ist nur bei einem normalisierten Materialfluss sinnvoll einsetzbar. Ausserdem können operative Eingriffe in das System den Kanban-Kreislauf stören. Sollten zudem sehr starke Bedarfsschwankungen auftreten, so ist es möglich, dass Kanban darauf nicht mehr ausgerichtet ist.
Einsatzmöglichkeiten
Das Kanban-System kann in einem Spital verwendet werden, um einen bedarfsorientieren Materialfluss zu gewährleisten und zu hohe Lagerbestände und somit auch die hohe Kapitalbindung zu vermeiden. In Kombination mit 5S weist das System ein grosses Potential für die Reduzierung nicht-wertschöpfender Prozesse auf. In den USA wird Kanban bereits seit einigen Jahren vor allem im Bereich der Organisation des Spitalalltags, zum Beispiel im Medikamentenmanagement, verwendet (Black & Miller, 2008). Mit Hilfe eines Kanban-Systems lassen sich Materialanforderungen aus dem Prozess heraus ableiten. Beispielweise können eingriffsbezogene Siebe im OP verwendet werden, um kostenträchtige hohe Materiallager zu vermeiden. Es lassen sich Verzögerungen und Fehllieferungen vermeiden und somit auch Stillstände und Wartezeiten im OP-Raum. Zusätzlich sinkt der Beschaffungsaufwand, dies führt auch zu einer Entlastung des Spitalpersonals.
Bitte zitieren Sie diese Quelle wie folgt:
Hollenstein, E. & Angerer, A. (2016). Kanban. In A. Angerer (Hrsg.), LHT-BOK – Lean Healthcare Transformation Body of Knowledge, Version 1.0. Winterthur. Abgerufen von www.leanhealth.ch
Literatur
Black, J. & Miller, D. (2008). Toyota Way to Healthcare Excellence: Increase Efficiency and Improve Quality wit Lean. Health Administration Press, 134–172.
Dickmann, P. (2009). Schlanker Materialfluss mit Lean-production, Kanban und Innovationen. Berlin: Springer.
Gabler Wirtschaftslexikon (o.J.). Kanban-System. In: Gabler Wirtschaftslexikon. Abgerufen von wirtschaftslexikon.gabler.de/Archiv/74282/kanban-system-v7.html.
Graban, M. (2012). Lean Hospitals - Improving Quality, Patient Safety, and Employee Satisfaction. 2. Auflage. New York: Productivity Press.
Lean Magazin. Effiziente Logistik mit Kanban. Abgerufen von: www.leanmagazin.de/lean-praxis/logistik/513-effiziente-logistik-mit-kanban.html
Slack, N., Brandon-Jones, A. & Johnston, R. (2014). Operations Management. 7. Auflage . Boston: Prentice Hall.
Wellman, J., Hagan, P. & Jeffries, H. (Hrsg.) (2011). Leading the lean healthcare journey: driving culture change to increase value. New York: Productivity Press
Zidel, T. (2006). A Lean Guide to Transforming Healthcare: How to Implement Lean Principles in Hospitals, Medical Offices, Clinics, and Other Healthcare Organizations. Abingdon: Taylor & Francis Group.
Zurück zur Toolsammlung