Energy Harvesting zum Aufladen des Akkus in einem RFID-Sensor-Label
Klimadatenlogger
Die Kühlkette in der Nahrungsmittel- und Pharmaindustrie braucht günstige und einfach bedienbare Klimadatenlogger. Um Temperatur und Luftfeuchtigkeit aufzuzeichnen, entwickelten wir ein biegsames Sensoretikett (Sensor-Label), das auf jede Verpackung passt. Als Stromquelle dient ein ausgeklügeltes Energy-Harvesting-System.
Einfach ein Etikett aufkleben, das fortlaufend Temperatur und Luftfeuchtigkeit misst und speichert: das wäre die wohl einfachste Technik, um die Kühlkette in der Nahrungsmittel- und Pharmaindustrie sicher zu überwachen. Ein Display braucht das intelligente Etikett nicht, dafür eignen sich NFC-fähige Smartphones oder spezielle RFID-Leser. Schwierig ist vor allem die Stromversorgung. Auf dem Markt sind heute einige semi-passive UHF-RFID-Datenlogger erhältlich, unter anderem von Phase IV, Intelleflex oder Caen RFID. Sämtliche Datenlogger sind batteriebetrieben, meist durch Knopfzellen, die eine Laufzeit von ein bis drei Jahren erlauben. Das Zentrum für Signalverarbeitung und Nachrichtentechnik hat stattdessen einen umweltfreundlichen, wiederaufladbaren und drahtlosen Datenlogger-Sensor entwickeln.
Einzigartig an dem vorgestellten flexiblen Datenlogger ist die Bauhöhe von weniger als 0,8 mm inklusive eines 0,2 mm dünnen und flexiblen Li-Ionen-Akkus, der per HF-Energy-Harvesting seine Energie drahtlos während des Auslesevorgangs bezieht. Die Kapazität des Akkus beträgt mit 1 mAh nur ungefähr 0,2 % einer Knopfzelle, daher war beim Design ein geringer Stromverbrauch besonders wichtig. Das Resultat war eine Laufzeit von über einem Monat. Bei jeder Interaktion mit einem UHF-RFID-Lesegerät lädt sich der Akku automatisch. Der Akku ist permanent gegen Tief- und Überladung geschützt.
Das Sensor-Label erlaubt lückenloses Überwachen der klimatischen Bedingungen. Temperatur und Luftfeuchtigkeit misst es mit dem Sensor-IC SHTC1 von Sensirion, das alle Anforderungen an Genauigkeit und Formfaktor erfüllt. Dabei stellt der UHF-RFID-Standard EPC Gen2 weltweite Kompatibilität sicher. Der Prototyp des Sensor-Labels im Bild unten ist auf einer flexiblen Leiterplatte aus Polyimidfolie aufgebaut.
Systemdesign
Das entwickelte System besteht aus dem Sensor-Label und einem UHR-RFID-Lesegerät. Mit dem Lesegerät identifizieren Anwender das Sensor-Label, konfigurieren die Messung, rufen die gesammelten Daten ab und laden den Akku, wobei alles drahtlos abläuft. Das Label misst präzise Temperatur und Luftfeuchtigkeit im konfigurierten Zeitintervall und speichert die Werte nichtflüchtig. Das Bild oben zeigt die Komponenten des Sensor-Labels.
Der UHF-RFID-Transponder bedient die Funkschnittstelle zwischen Label und Leser. Er ist verantwortlich für die Datenübertragung und das Gleichrichten der hochfrequenten Wechselspannung. Die gleichgerichtete Spannung dient dem Energy Harvester als Quelle und gleichzeitig als Wake-up-Signal für den Mikrocontroller. Damit ist die MCU immer aktiv, sobald das Sensor-Label ein Funksignal ausreichender Feldstärke erhält. Das Harvester-IC erfüllt verschiedene Funktionen. Es lädt den Li-Ionen-Akku, solange die Feldstärke dazu ausreicht und der Akku noch nicht voll ist, und es beinhaltet einen Spannungsregler zum Versorgen von Mikrocontroller (MCU) und Real-Time-Clock (RTC). Um den Stromverbrauch zu senken, wird der Temperatur- und Luftfeuchtesensor nur während einer Messung durch die MCU mit Strom versorgt.
Messzyklus
Die RTC startet Messungen unabhängig vom HF-Feld. Nach einem Wake-up fragt der Mikrocontroller vom Sensor Temperatur und Luftfeuchtigkeit ab, speichert diese im nichtflüchtigen Speicher und geht nach wenigen Millisekunden auf Standby zurück. Auf Abruf vom Lesegerät sendet die MCU die gesammelten Daten durch den Transponder.
Eckdaten
Im Standby zwischen den Messungen beträgt der Stromverbrauch von Harvester, MCU und RTC kombiniert lediglich 1 µA. Der Transponder wird nicht vom Akku versorgt und trägt dadurch nicht zum Standby-Verbrauch bei. Der Stromverbrauch im aktiven Modus ist vernachlässigbar aufgrund der extrem kurzen Dauer einer Messung im Verhältnis zu den Standby-Phasen. Damit lässt sich die Laufzeit des Li-Ionen-Akkus mit 1 mAh Kapazität auf rund sechs Wochen bestimmen. Drückt der Anwender auf einen Taster oder unterschreitet der Akku die Tiefentladungsgrenze, dann schaltet der Harvester die Versorgungsspannung ab und versetzt das Sensor-Label in den Tiefschlafmodus. Hier sinkt der Stromverbrauch auf typisch 10 nA. In diesem Modus lassen sich ungenutzte Labels über Jahre lagern, ohne dass der kleine Li-Ionen-Akku tiefentladen wird.
Das Sensor-Label arbeitet semi-passiv: der Transponder bezieht seine Energie direkt aus dem HF-Feld, der Akku versorgt alle übrigen Komponenten. Deswegen muss während des Datentransfers ein HF-Feld anliegen. Die Modulation und das Kommunikationsprotokoll entsprechen EPC Gen2. Temperatur und Luftfeuchtigkeit kann das Label in benutzerdefinierten Intervallen von 1 s bis zu 4 h loggen, mit einer wählbaren Startzeit der ersten Messung. Der Mikrocontroller kann bis zu 8000 Datensätze speichern. Datenloggen mit hoher Genauigkeit ist in einem Temperaturbereich von -10 bis +50 °C und einem Bereich relativer Luftfeuchtigkeit von 0 bis 100 %RH garantiert.
Flexible Leiterplatte
Um Platz zu sparen und eine zuverlässige Fertigung sicherzustellen, sollte das Design mit der kleinstmöglichen Anzahl Komponenten auskommen und möglichst wenig Strom verbrauchen. Um künftig auch Aufkleb-Labels zu ermöglichen, war eine einseitige und flexible Leiterplatte ohne Durchkontaktierungen nötig, was an ein hochfrequenztaugliches Layout einige Anforderungen stellt. Das ganze Label sollte maximal 0,8 mm hoch sein, um biegsam zu bleiben.
Die Dipolantenne wurde durch eine Simulation für das europäische UHF-RFID-Frequenzband von 865 bis 870 MHz dimensioniert. Im Bild unten ist ein Funktionsmuster des Sensor- Labels zu sehen, mit der Antenne am oberen Rand. Die Antenne ist gefaltet, damit das Label so klein wie eine Kreditkarte bleibt. Die Anpassung der Antennenimpedanz von 50 Ohm auf die Eingangsimpedanz von (31 -j320) Ohm des SL900A (heute AMS SL13A) wird durch eine einzige Induktivität von 33 nH erreicht (L2 in Bild 4). Alle Komponenten inklusive Akku sind in ausreichendem Abstand zur Antenne platziert, um deren Abstrahlcharakteristik nicht zu sehr zu beeinflussen.
Als Mikrocontroller wählten wir einen MSP430FR5749 von Texas Instruments. Das nichtflüchtige FRAM (Ferroelectric RAM) bietet Speicherplatz für 16 kByte Daten, dazu weniger Stromverbrauch, schnelleres Schreiben und mehr Schreibzyklen als die verbreiteten Flash-Speicher. Die Daten werden nicht etwa magnetisch gespeichert wie der Name suggeriert, sondern mittels Kristallen mit ferroelektrischen Eigenschaften. Durch die externe RTC lässt sich der Stromverbrauch im Standby weiter senken. Die Auflade-LED (rot im Bild unten) leuchtet, wenn Energy Harvesting stattfindet, was bei ausreichender Feldstärke im UHF-Bereich der Fall ist. Die Log-LED dient zum Signalisieren verschiedener Label-Zustände mit kurzen Blitzen, etwa wenn ein Wake-up stattfindet.
Harvester
Für das Energy Harvesting ist der MAX17710 von Maxim zuständig, da er ab einer Eingangsspannung von 0,75 V und einer Eingangsleistung von 1 µW mit dem Harvesten beginnt. Außerdem benötigt dieses IC kaum externe Komponenten zur Konfiguration. Bild 4 zeigt den Energy-Harvesting-Schaltungsteil des Sensor-Labels. Am VPOS-Pin des RFID-Transponders liegt die gleichgerichtete Spannung an. Die Versorgungsspannung für den Messteil ist auf 2,3 V geregelt.
Sobald VPOS eine Spannung von 0,75 V plus 1,6 V Flussspannung von D2 übersteigt, beginnt das Energy Harvesting und der Akku wird geladen. Dies funktioniert bis zu einer Distanz von 40 cm zwischen dem Label und einem Leser, der mit 1 W HF-Leistung sendet. Über weitere Distanzen im Meterbereich können Anwender das Label immer noch abfragen, aber die LED D2 unterbindet das Laden des Akkus schon vorher: Die Sensitivität des Transponders nimmt nämlich ab, wenn er bei knapper Energie auch noch den Harvester versorgen muss. Außerdem stellten wir fest, dass ein stabiles Aufstarten des Harvester-Chips von Maxim im HF-Feld nur bei einer Quellenspannung kleiner als 1 V stabil funktioniert.
Akku schützen
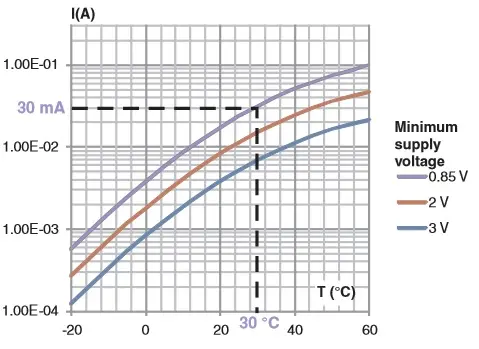
Um den Harvester zu aktivieren und in den gewünschten Betriebsmodus zu versetzen, muss eine Pulsfolge an den Pins AE und LCE anliegen. Weil der Mikrocontroller diese Aufgabe im spannungslosen Anfangszustand nicht übernehmen kann, erzeugt ein Flankendetektor diese Pulse. Nach Aktivierung befindet sich der Harvester im Zustand AE und LCE Active (siehe Datenblatt MAX17710), in dem er einerseits genügend Strom liefert und andererseits eine Abschaltung aktiviert, wenn der Akku einen Unterspannungswert von 3 V erreicht. Letzteres schützt den Akku bei kleinen Arbeitsströmen korrekt.
Flache und biegbare Li-Ionen-Akkus sind noch nicht sehr verbreitet. Wir testeten eine Thinergy MEC201 von Infinite Power Solutions, die derzeit nicht mehr erhältlich ist, eine Enfilm EFL700A39 von ST Microelectronics und einige flache, jedoch nicht biegsame Produkte von Powerstream und Jinke Energy Development.
Um die Funktion des Sensor-Labels bei Temperaturen unter 0 °C zu gewährleisten, ist ein großer Stützkondensator zwischen Akku und Spannungsregler nötig, weil der Innenwiderstand bei flachen Li-Ionen-Akkus mit sinkender Temperatur stark zunimmt. Diese Eigenschaft ist im Bild am Beispiel des Li-Ionen-Akkus EFL700A39 dargestellt. Ein Innenwiderstand von mehr als 1 kOhm bei -10 °C ist nicht unüblich, was nicht mehr ausreicht, um den Einschaltstrom für den Mikrocontroller zu liefern, wobei Spitzenströme von über 35 mA auftreten. Deshalb stammt die Energie für die kurze Messdauer aus dem Stützkondensator, welcher sich anschliessend im Standby über lange Zeit wieder auflädt. C7 ist so dimensioniert, dass die Spannung im Betrieb bei der tiefsten Temperatur in keinem Fall unter die 3-V-Unterspannungsgrenze sinkt. Der Ladestrom in den Akku nimmt bei tiefen Temperaturen ebenfalls ab.
Wirkungsgrad des Transponders
Das Sensor-Label lässt sich mit einem tragbaren UHF-RFID-Leser mit 1 W Sendeleistung (EIRP zirkular) über eine Distanz von einem Meter auslesen. Der Li-Ionen-Akku wird bis zu einer Distanz von 40 cm über die Luft aufgeladen, bei Temperaturen über +10 °C. Bei einer Distanz von 20 cm und der Arbeitsfrequenz von 868 MHz beträgt die Freiraumdämpfung 17 dB. Das zirkular polarisierte Feld des Lesegeräts hat den Vorteil, dass eine axiale Rotation des Sensor-Labels die Empfindlichkeit nicht beeinträchtigt. Nachteilig ist ein systembedingter Verlust von 3 dB beim Empfang mit einer Dipolantenne. Demnach erreichen den Transponder von der abgestrahlten Leistung noch ein Zehntel, also 10 mW, was eine Messung mit dem Spektrumanalysator an der Antenne bestätigt. Am Gleichrichterausgang des Transponders ließ sich für diesen Fall eine verfügbare Leistung von etwa 2 mW messen.
Der Wirkungsgrad des Transponders beläuft sich somit auf 20 %. Die LED D2 reduziert die Leistung auf ein Viertel. Diesen Nachteil haben wir in Kauf genommen, weil das Label so mit nur einem Bauteil (LED D2) das Energy Harvesting bei kleiner Empfangsleistung abstellt. Der Vorteil ist eine höhere Reichweite zum Steuern und Auslesen des Sensor-Labels. Der Harvester sieht also eine Eingangsleistung von 0,5 mW und lädt den 4-V-Akku noch mit 0,1 mW respektive 25 µA, was einem Wirkungsgrad von 20 % entspricht. Das Laden der vollen Akkukapazität von 1 mAh über eine Distanz von 20 cm dauert also 40 h. Bei halber Distanz halbiert sich auch die Ladezeit ungefähr. Der gesamte Wirkungsgrad des HF-Energy-Harvesting auf dem Sensor-Label von der Empfangsleistung am Transponder bis zur Ladeleistung des Li-Ionen-Akkus beträgt gerade noch 1 %.
Dass der Wirkungsgrad derart klein ausfällt, hat einerseits mit den Einschränkungen beim Design zu tun. Andererseits nimmt der Wirkungsgrad von Gleichrichter und Harvester bei kleinen Leistungen stark ab, weil Schalt- und Diodenverluste immer mehr zum Tragen kommen. Durch Verwendung anderer Harvester-Chips mit mehr Bauteilen und effizienterem HF-Gleichrichter im oder zusätzlich zum Transponder lässt sich der Wirkungsgrad erhöhen. Zweifellos befindet man sich erst am Anfang von effizienten Sensor-Labels und die Zukunft wird Transponder mit HF-Harvester auf einem Chip bringen.
Auf einen Blick
Beteiligte Institute und Zentren:
Projektpartner:
Finanzierung: KTI
Projektstatus: beendet