Automatic control cabinet wiring in a human-robot cooperation
Electrical control cabinets, for example for controlling larger machines or other technical systems, are usually very individually tailored to the specific intended use and are therefore only identical in small series. Today, these control cabinets are almost exclusively assembled and wired manually. Despite small series and sometimes high complexity of the task, there is a desire to be able to produce control cabinets as automatically as possible. A few years ago, the company W.Althaus AG from Aarwangen brought a machine onto the market (ATHEX) for the fully automatic assembly of cabinets with electrical components. However, automatic control cabinet wiring was previously too complex to be implemented reliably and cost-effectively. After unsuccessful attempts with prototypes from foreign manufacturers, the company W.Althaus AG turned to the robotics specialists at the IMS at the ZHAW.
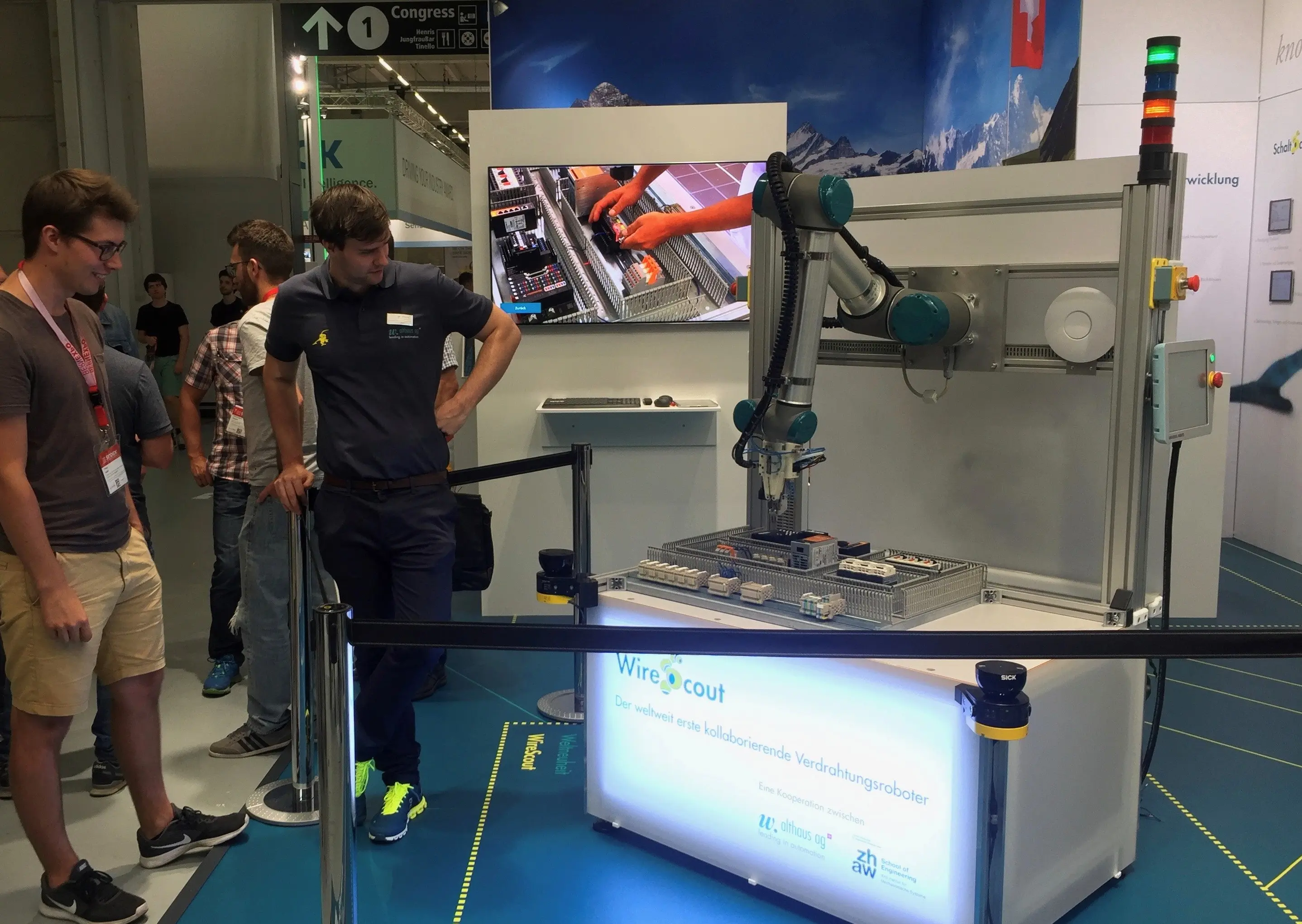
Together, in a project funded by the Swiss Agency for Innovation Promotion (KTI, now Innosuisse), a functional prototype was developed, which is capable of reliably wiring control cabinets fully automatically as part of human-robot cooperation. The cooperation scenario allows a skilled worker to intervene at any time in the otherwise fully automatic wiring process if exceptional situations arise. For example, when processing slack parts, such as the strands for wiring, it cannot be completely prevented that the laid wires occasionally jump out of the cable ducts and thus hinder the further wiring process. This is where the worker's helping hand is needed to quickly and easily give the robot a hand(s). This type of collaboration between humans and industrial robots is only possible if the system is equipped with the necessary safety concept and the corresponding sensors. The information about the wiring is obtained directly from the electrical planning software (EPLAN) data used for planning the control cabinet, i.e. the robot paths required for laying the strands are generated by the WireScout system itself without any additional programming effort. Since the geometric dimensions in the individual control cabinets are almost never plan-accurate, 2D and 3D sensors ensure individual adjustment of the robot target positions during the ongoing wiring process. This makes it possible to insert the strands into the connection locations reliably and with an accuracy of less than a millimeter.
Projekt details
Project reference:
25306.2 PFIW-IW
Funding: KTI (now Innosuisse)
Project start: 2017
Project duration: 18 months