Process Engineering
The laboratory of process engineering develops new and optimizes existing procedures and processes.
The core areas are separation processes, material conversion as well as particle technology and catalytic processes. We focus on the industrialization of new processes and the intensification of existing ones. Modern installations and equipment on a laboratory and a pilot scale as well as state of the art analytical instrumentation support our research and our inspiring and applied teaching.
Process Development
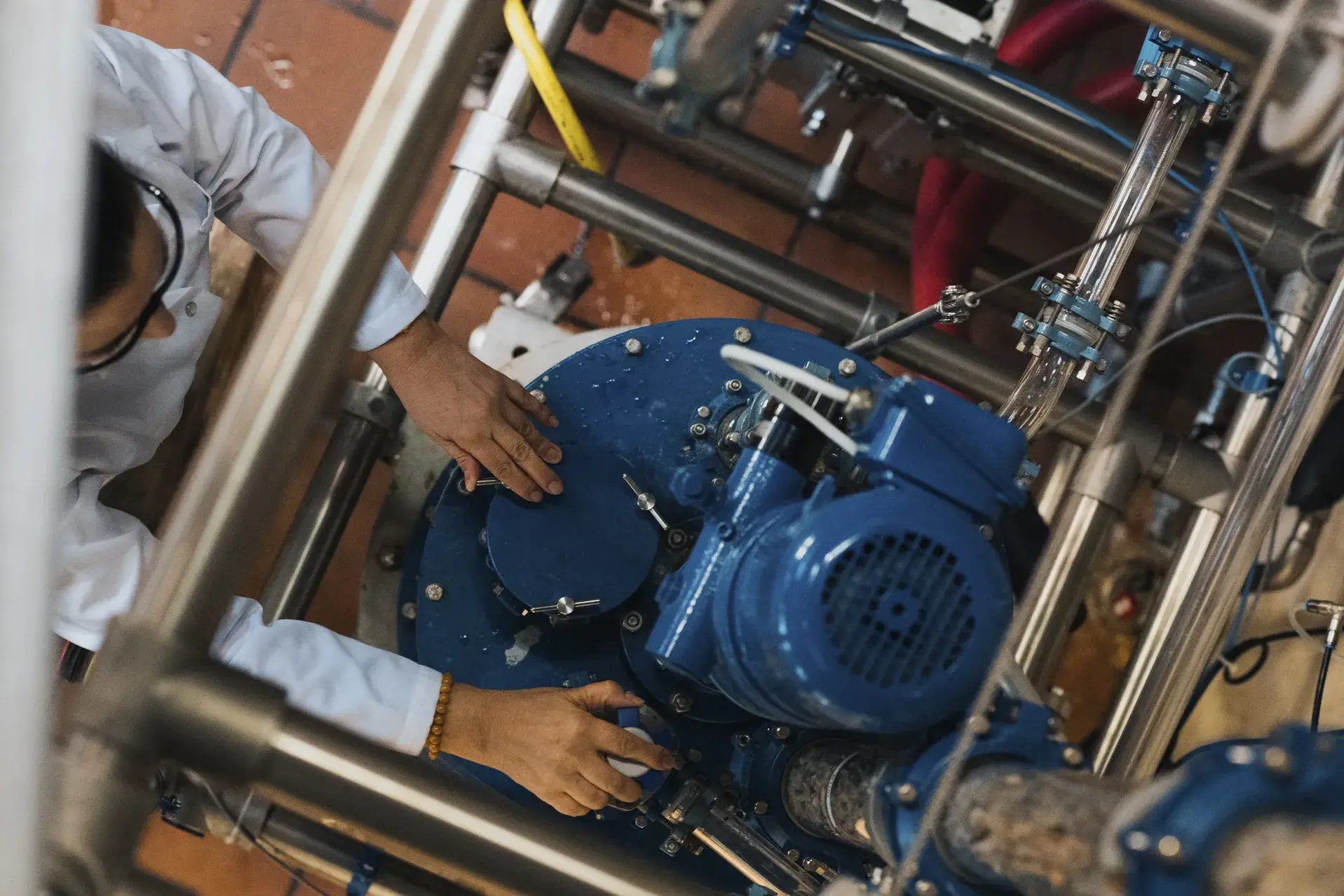
The Process Engineering Laboratory is involved in process engineering research. Our focus is on the production and application of functional materials, chemicals and fuels, as well as process development and analytical process monitoring. We pay particular attention to sustainable and environmentally relevant topics such as air and waste gas purification, conversion processes for bio-based raw materials, recycling processes and the circular economy. We are also committed to transferring current applied research directly into teaching.
We are developing technologies for efficient CO₂ capture and conversion, as well as processes for sustainable fuel production. We also focus on the treatment of gases, exhaust gases and wastewater. In addition, we work on processes for material separation, in particular extraction with supercritical CO2, and the synthesis of particles, catalysts and metal-organic frameworks (MOFs).
In process development, we focus on thermal and mechanical separation processes, chemical conversion processes and the production and encapsulation of particles. Our expertise includes reaction engineering, scale-up and process intensification to make industrial processes more efficient and environmentally friendly. This includes supporting the transition from batch to continuous processes. Recycling and product work-up are also part of our research, as is the development and application of catalysts for energy and environmental technologies.
To put these innovative processes into practice, we have state-of-the-art laboratory equipment and pilot plants. These include multi-functional reactors with volumes of up to 50 litres (Fig. 1) and rectification and evaporation units with capacities of up to 250 litres. We also use membrane and mechanical separation processes and a supercritical extraction and impregnation unit at up to 450 bar. We also use thermal and pressure swing sorption processes, and our explosion-proof facilities ensure the highest safety standards.
Process and Materials Analysis
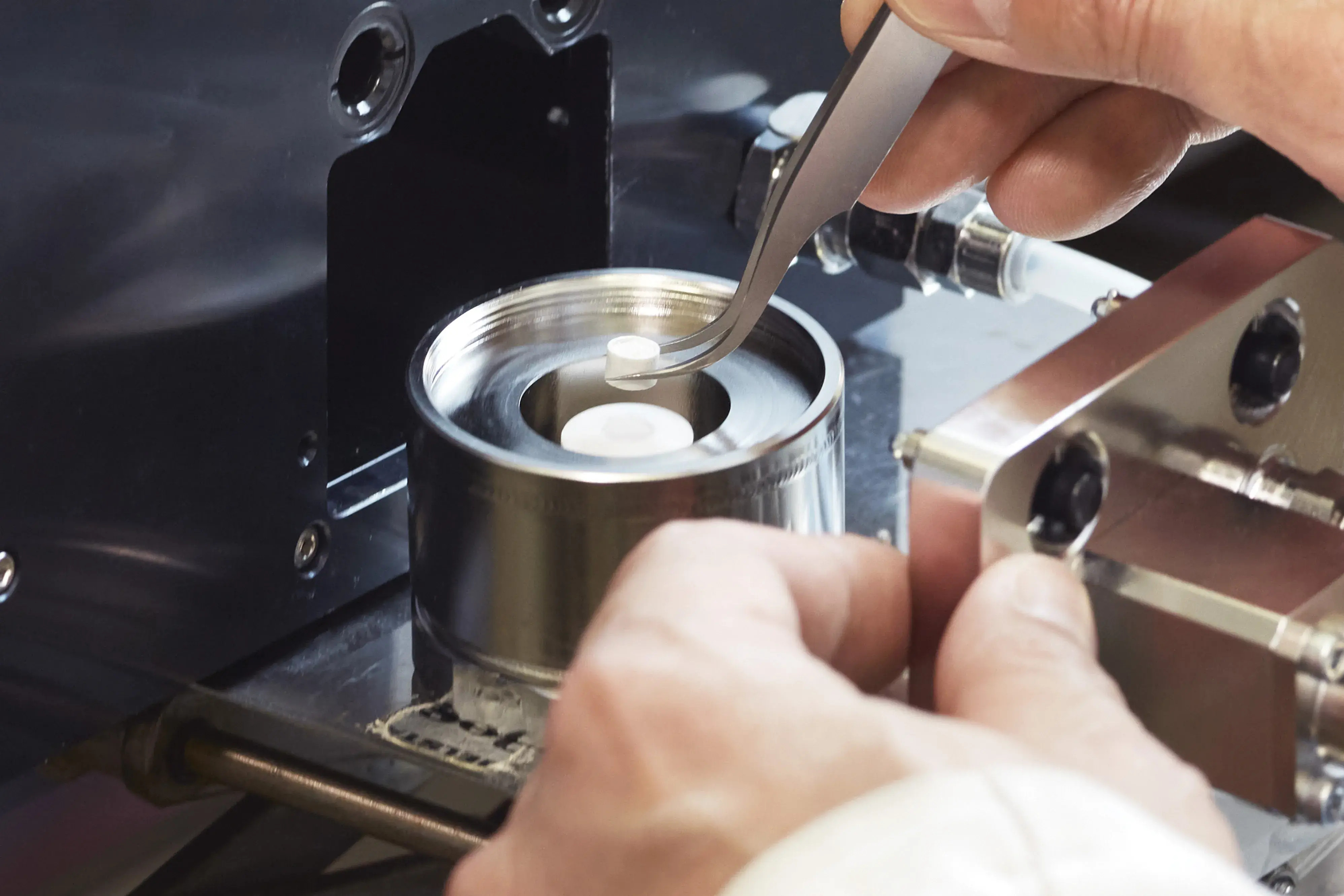
Process and materials analysis is the basis for the development of efficient and sustainable process engineering. Our laboratory uses modern process analytical technologies (PAT) to research new processes, to develop industrial processes and to monitor and control processes accurately. Online, inline, atline and offline PAT techniques play a central role. They enable comprehensive data collection that helps to improve product quality and maximise efficiency.
We focus on the study of chemical processes at the molecular level using infrared, Raman, UV/VIS and mass-spectroscopy to analyse processes in-situ and obtain real-time data. We also analyse parameters such as temperature, pressure, concentration, and flow behaviour to make processes efficient and stable. Preparative and analytical chromatography methods such as HPLC, ion chromatography, GC-FID, GC-headspace, and GC-MS enable us to purify and quantify products. The data obtained helps us to design process conditions that are both economical and environmentally friendly, and to ensure consistently high product quality.
In materials analysis, we use high-precision technologies to characterise raw materials, intermediates, end products and catalysts. Analysis of particle size, surface structure and chemical composition is critical to achieving the desired properties for specific applications. We use molecular spectroscopy (e.g. Raman, FT-IR, ATR-FTIR, DRIFTS (Fig. 2), MES-DRIFTS, UV-VIS, MS), elemental analysis (e.g. ICP-OES, SEM-EDX) and techniques such as X-ray diffraction (XRD), scanning electron microscopy (SEM) and thermal analysis (TA) to investigate the structural and chemical properties of materials.
By closely linking process and material analysis, we lay the foundation for innovative and resource-efficient processes. Our chemical analytical techniques make a significant contribution to improving the efficiency and sustainability of novel processes.
Applications
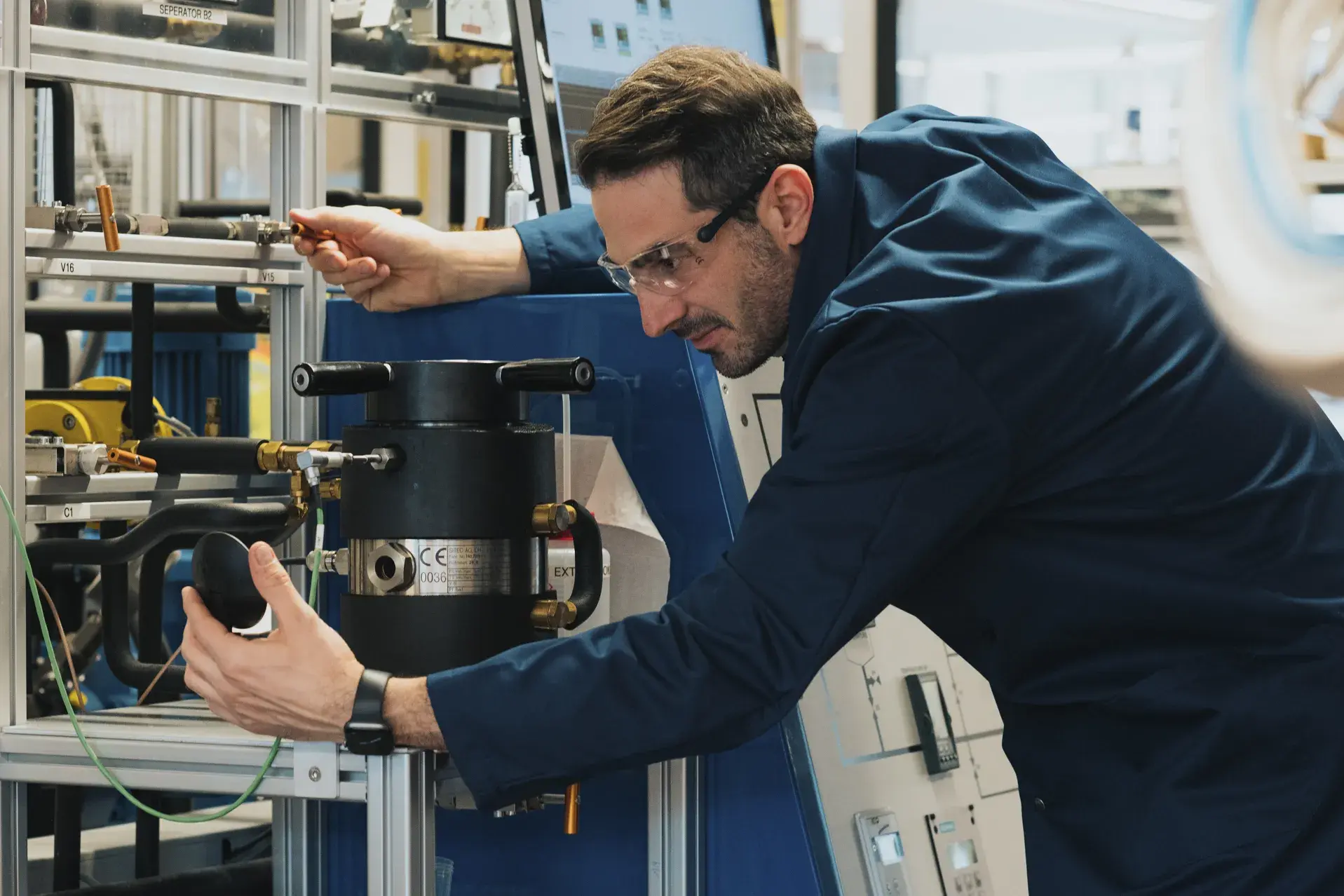
The current focus is on processes in which bio-based raw materials are used to develop sustainable aviation fuel or innovative, sustainable materials. For example, the VOC absorption capacity of lime-bound plaster based on biochar is being analysed in order to provide environmentally friendly construction products. We are also researching the extraction of isoprene from renewable resources for polymer production and catalytic fuel processing for solid oxide fuel cells (SOFC).
Efficient sorption materials is another mainstay of our research. Our research has contributed to the development of sorption materials such as highly efficient three-dimensional ceramic surfaces for CO₂ capture. MOFs were also researched in collaboration with industry for CO₂ separation and successfully used in pilot plants.
In safety engineering, one project concerned the dimensioning of NH₃ emergency scrubbers to ensure efficient ammonia purification. Process safety was also an important aspect in the development of an experiment-based design tool for continuous reactors.
In addition, we helped to optimise a process for the efficient production of insect-pathogenic granulosis viruses to promote innovative and sustainable plant protection.
A key success factor has always been the use of our laboratory equipment and pilot plants combined with modern analytical methods. By using our IR cell for inline monitoring of extractions with supercritical CO2 (Fig. 3) and in-situ IR spectroscopy to elucidate the reaction mechanisms of catalytic exhaust gas converters, we have been able to streamline product developments.
We have also co-developed and utilised innovative 3D-printed ceramic structures for highly efficient mass transfer in separation columns. These applications illustrate the versatility and effectiveness of our activities as well as the decisive contribution of our laboratory and pilot plants for successful realisation in industry.