Ceramic Materials
In the laboratory of ceramic materials, the complete process chain of synthesis and production of advanced ceramic materials for industrial applications can be reproduced on a prototype scale. A broad range of relevant ceramic materials and production processes is subject of investigations.
The main technical focus of the lab lies on the development of innovative ceramic shaping methods and synthesis of tailored ceramic materials for demanding applications in mechanical, medical and chemical engineering. A comprehensive, universal and modern infrastructure supports the activities.
Production of ceramics
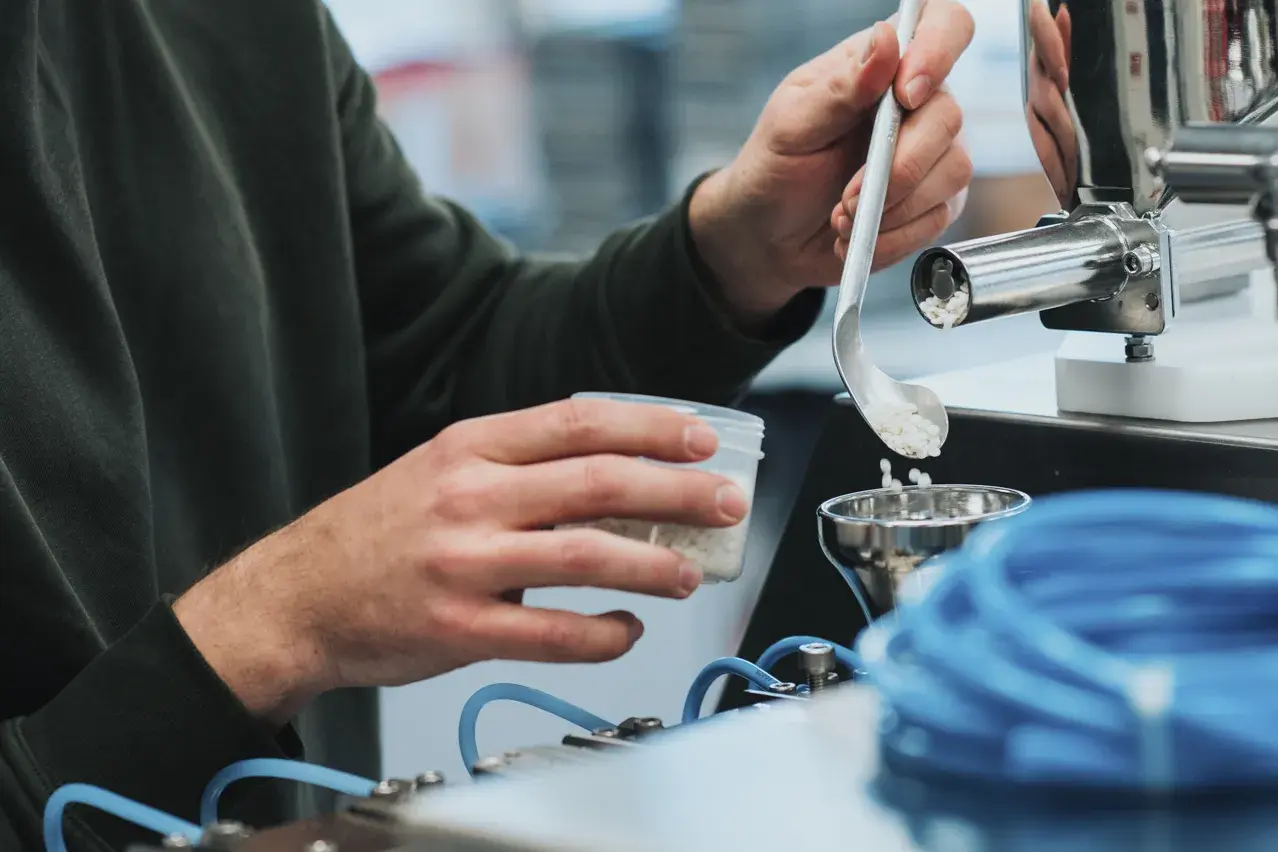
We have many years of expertise and equipment at our disposal to cover the entire process chain for manufacturing ceramics for use in mechanical engineering, medical technology, electrical engineering or process engineering, from laboratory scale to pre-series prototypes. Our many years of experience and our laboratory and technical key equipment allow us to react flexibly to the respective requests of our industrial partners and to select and implement the most suitable solutions in each case.
The production of ceramics begins with the selection of raw materials. If necessary, we have the chemical expertise to synthesize particles, powders or granulates with a specified composition ourselves. We use solid-state reactions, precipitation reactions, colloidal processes and even microfluidic techniques.
The particle surfaces often have to be chemically modified for further processing. We have many years of experience in the selection of suitable process additives such as dispersing agents, plasticising aids, defoamers, binders, etc.
We develop our own formulations and binder recipes for coatings, resin-based additive manufacturing processes, molding, injection molding or for the production of polymer-derived ceramics.
We are proficient in all common shaping methods in ceramics, i.e. plaster casting, injection molding, tape casting, gel casting, pressing and extrusion from laboratory to pilot plant scale. For example, we have two industrial injection molding systems, a roll-to-roll coating system and twin-screw extruders in various dimensions and performance classes.
In addition, additive manufacturing methods/ 3D printing have played an important role in the realization of development projects in recent years. All relevant technologies are available in our laboratory for the additive manufacturing of ceramics - DLP digital light processing, SLA stereolithography, powder printing/binder jetting, MEX granulate microextrusion. We are continuously developing new innovative processes for the additive production of ceramics in student projects.
With the exception of vapour deposition, ceramic coatings are also part of our portfolio. We have experience with polymer-derived ceramic coatings, sol-gel coatings, enamels and glazes.
Finally, ceramic production by definition includes the sintering process in high-temperature furnaces. We can realize maximum sintering temperatures of up to 1800 °C, if required under vacuum, inert or other gas atmospheres.
Characterization
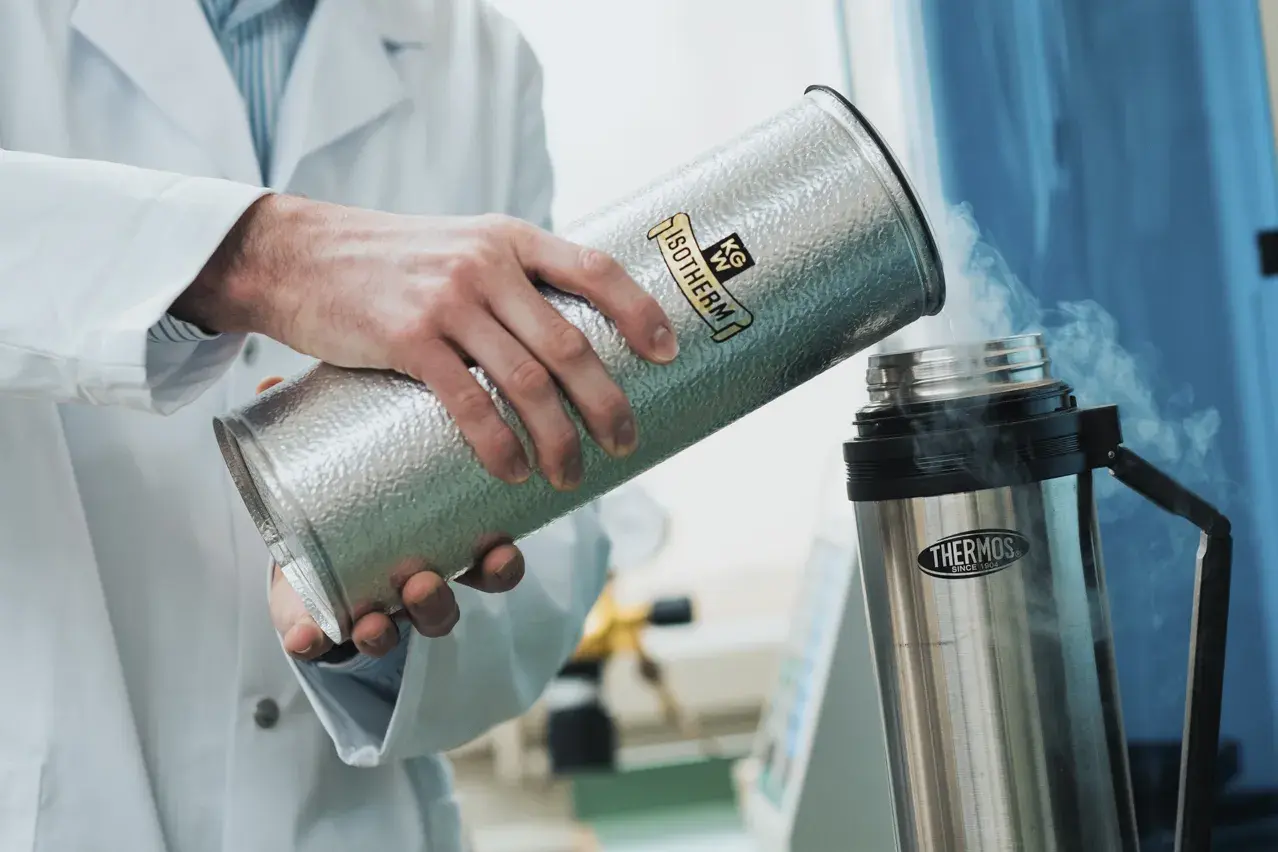
The basis for the development of new ceramic materials, applications and systems is analytical equipment adapted to the respective issues. The Laboratory for Ceramic Materials has a comprehensive portfolio of methods for characterizing raw materials, semi-finished products and products.
Compositional analysis includes crystal structure analysis and mineralogical composition of powders and ceramics (X-ray diffraction XRD) as well as chemical composition (EDX in SEM, high-pressure digestion methods with subsequent ICP-OES analysis). If required, we also have comprehensive spectroscopic equipment (UV-VIS, IR, Raman, XPS).
Various particle analyzers are available for investigating the morphological properties and particle size distributions of powders - laser diffraction, DLS, wet, dry, microscopy, sieve analysis, gas adsorption BET, SEM. The development of dispersions, pastes and plastic masses is supported by rheological analysis methods if required.
The key to understanding drying, debinding and sintering processes is thermal analysis. We use simultaneous thermal analysis systems DTA/DSC/TG with coupled gas analysis (IR, MS) and dilatometers (horizontal, vertical, optical). In addition, there is the possibility of thermal analysis of phase transformations in XRD using a furnace that can be used up to 1600 °C (in a vacuum) and special light microscopes.
Due to the special properties of technical ceramics - high strength combined with brittle fracture behavior - the mechanical characteristics of ceramics must be tested and examined using adapted test procedures and statistical methods (Weibull statistics). Various testing facilities and tools are also available for this purpose.
The technical properties of ceramics are determined by microstructure and defects. We have many years of experience in sample preparation and electron microscopy.
Other application-specific testing methods include the characterization of surfaces (confocal microscopy, AFM), porosity and permeability, electrical conductivity, etc. A comprehensive list of the analytical infrastructure available at IMPE can be found here.
Applications
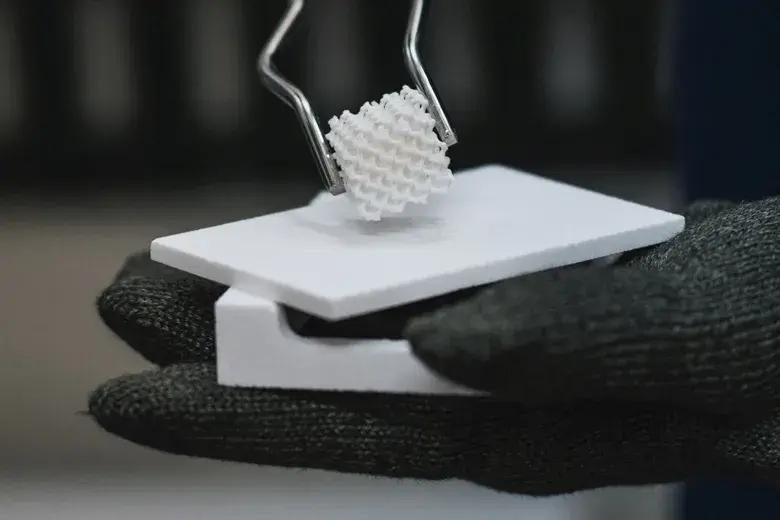
Technical ceramics are used as functional materials in a wide range of industrial applications. Thanks to our many years of experience in cooperation with our industrial partners from various sectors, we can cover a wide range of application areas. In the past, for example, we have successfully completed projects in the following areas:
Chemical process engineering offers a broad field of application for highly specialized and tailor-made ceramics, e.g. for applications in catalysis, separation (membranes, filters), or adsorption. In recent years, various projects have been successfully implemented in these areas, for example for the additive manufacturing of ceramic distillation columns, customized diaphragms for pH sensors, air filters for particle and virus filtration or the development of additively manufactured CO2 adsorption bodies.
In the field of materials for energy technology, various SOFC fuel cell technology projects have been worked on in the past and anode materials for lithium batteries have been developed in the field of electrochemical storage.
For applications in medical technology, for example, we have been able to develop dental implants with osseofunctional surfaces or realize somewhat more exotic applications such as targets for radionuclide therapy.
Mechanical engineering is a classic field of application for high-performance ceramics due to the special properties of these materials. We support our partners in material selection and product development through to the production of pre-series using ceramic powder injection molding. Examples of such development partnerships include the development of ceramic heating elements, ceramic insulators for welding technology or ceramic-bonded grinding wheels.