Project Example: Measurement, Calibration & Modelling of High Performance Polymers
In order to determine the mechanical material parameters of polymers, various material tests are generally carried out in order to adapt the determined stress-strain curves to a suitable material model using computer software.
At IMES, the laboratory infrastructure exists to carry out the material tests necessary for polymer materials in order to analyse static, dynamic and/or thermomechanical material behaviour. A high level of expertise according to the current state of research and many years of experience in the calibration of a wide variety of material models from experimental data and their application in numerical system simulations round off the range of services.
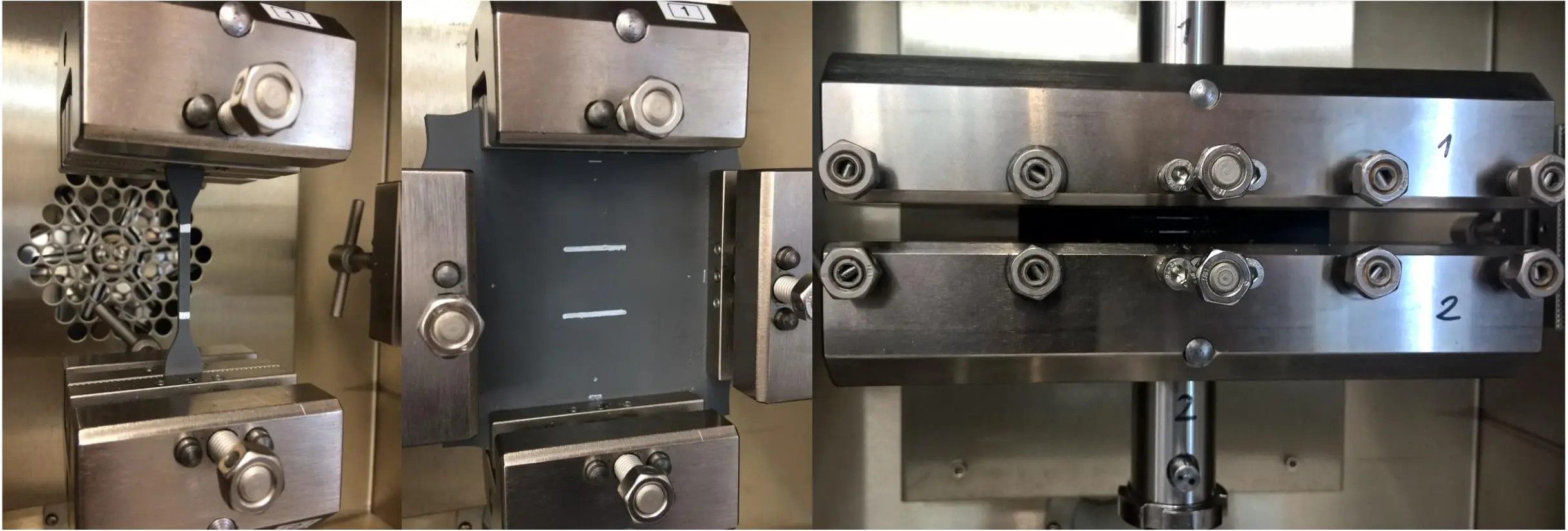
For example, even in the quasi-static analysis of elastomers, the experimental determination of the stiffness parameters is challenging because the generally large coefficients of friction of rubber materials falsify the measurement results. In a uniaxial compression test, it is not possible to generate an homogeneous stress state due to the high static friction between the specimen and the clamping. Also, in equibiaxial tensile tests, stress inhomogeneities arise due to the test setup, which usually cannot be neglected.
At IMES, a procedure exists to eliminate the influence of friction in the measurement results with the help of non-linear mathematical optimisation algorithms. This allows very realistic stiffness parameters to be derived from elastomer samples with simple (friction) test setups, which describe the mechanical and thermal behaviour of rubber materials very well within the framework of suitable material models.

The procedure represents an efficient method for mechanically characterising any elastomer compounds and feeding them into realistic numerical simulations of any component geometries, for example by employing the finite element method (FEM).
Application example: Inflatable hose seal
For a static simulation of an inflatable seal made of a silicone, an hyperelastic material model (Ogden 3rd degree) was created. For this purpose, three different material tests (uniaxial tension, equibiaxial tension, planar tension) were carried out in order to determine the corresponding material parameters from the stress-strain curves to describe a generally valid isotropic material behaviour. In the case of the equibiaxial test, stress inhomogeneities arise in the corners of the square specimen due to the test setup. These are corrected by an optimisation procedure in which the force-displacement curves from the test are matched with an FE model.
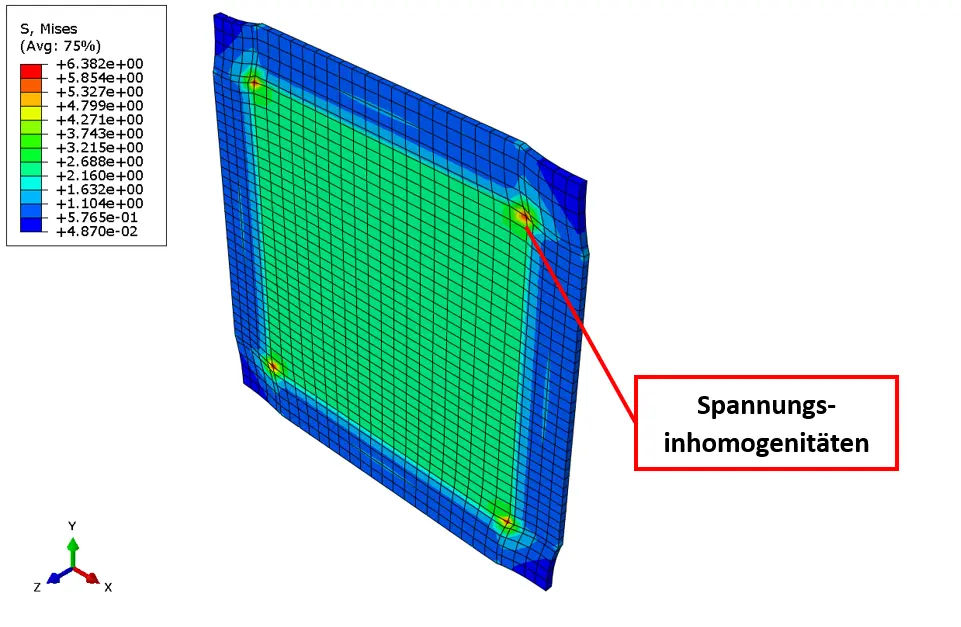
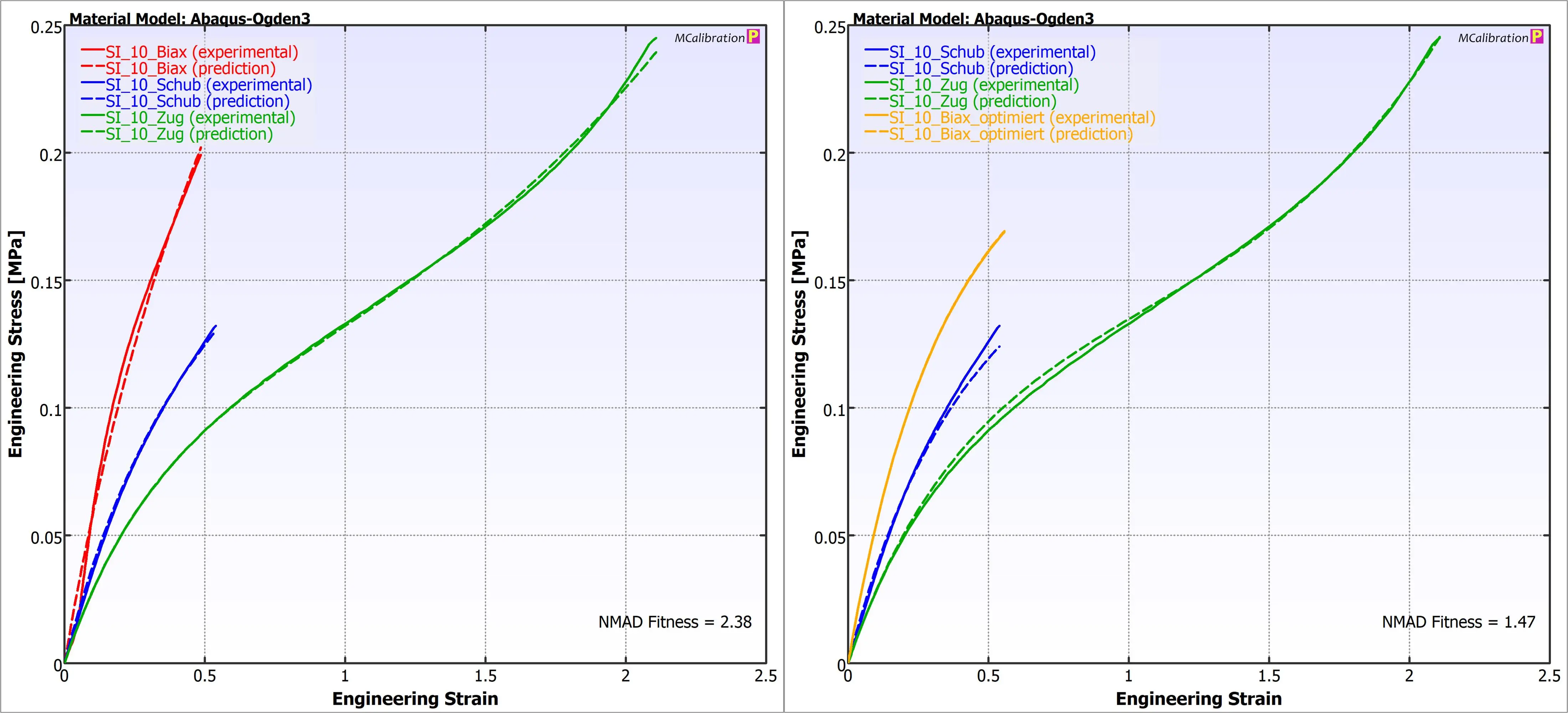
The material model was tested with a 2D simulation in which a cross-sectional geometry of the hose was inflated by increasing the internal pressure to seal the gap between the hose and the top plate.
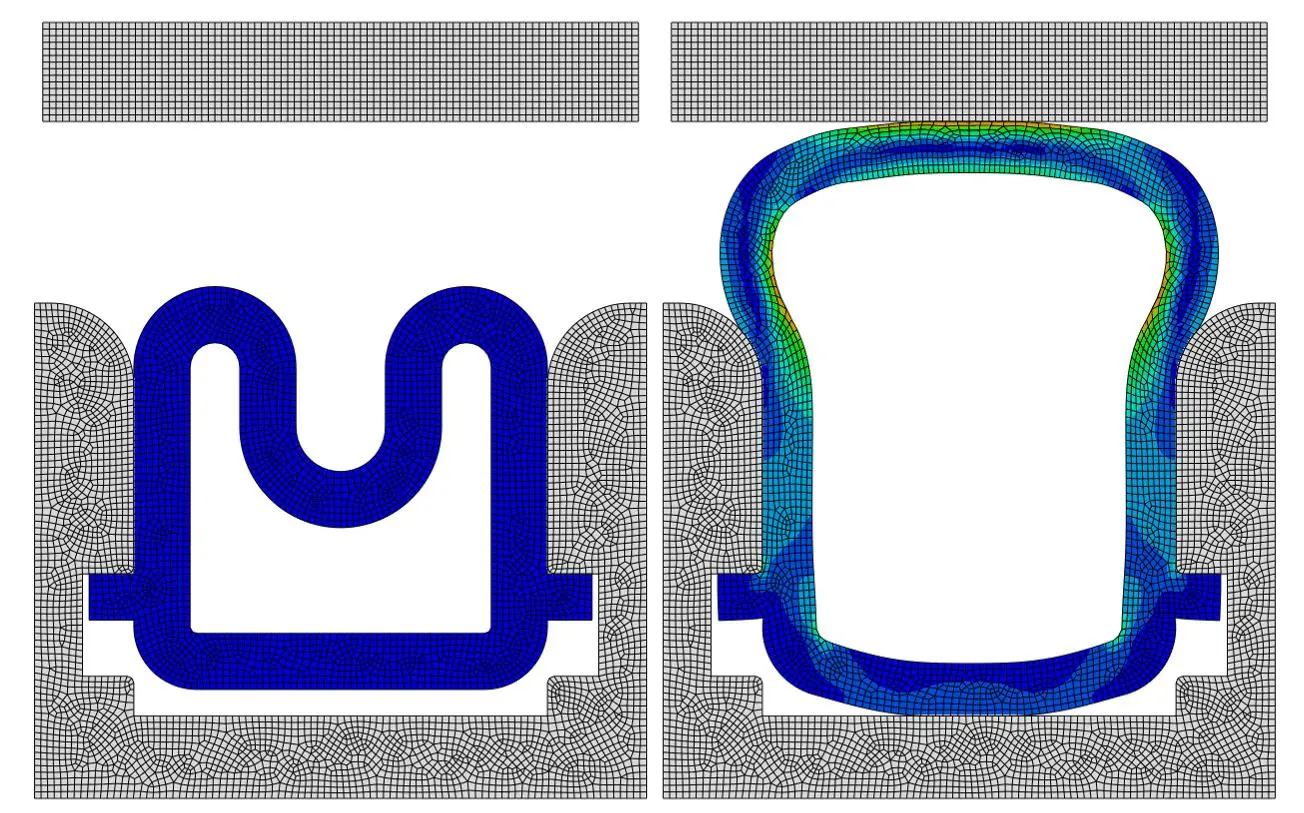
This simulation is numerically demanding due to the large displacements. In particular, the "turning upside down" of the hose contour poses a stability problem. Due to the strongly non-linear relationship between the load and the resulting displacement, this type of problem cannot be solved by a linear increase of the internal pressure and requires more specialised displacement-controlled calculation methods (arc length method).
Application example: Roller spring
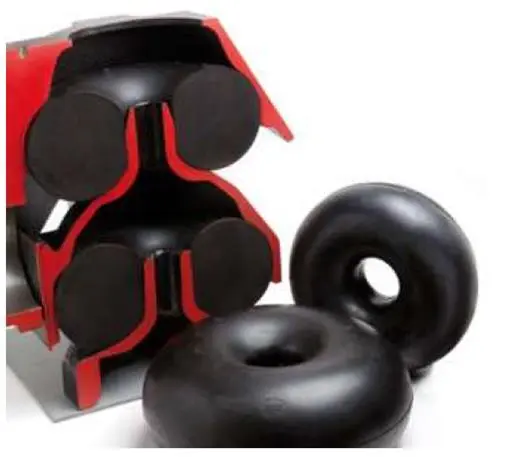
For a roller spring with an area of application in the railway industry (manufacturer Borflex Rex SA, www.borflex-rex.ch), a new rubber compound with flame protection was developed with Compounds AG (www.compounds.ch). The fire-protective properties are achieved in elastomer-based components by adding special fillers and additives. However, this also leads to a significant deterioration of the mechanical and dynamic-mechanical properties. Especially for dynamically stressed components such as the roller spring, it is still a great challenge to produce a flame-retardant elastomer compound that has the required mechanical material properties.
The mechanical properties of the flame-retardant elastomer were compared with a reference compound without flame retardancy by means of various mechanical tests on reference plates and on the finished part.
In order to characterise the relationship between compound and component properties by means of FEM, time-dependent viscoelastic-plastic material models were created for the compounds. In addition to the three quasi-static tests as in the previous application example, drop tower tests with increased strain rates as well as measurements of the compression set were used for calibration. With these models, the time-dependent material properties such as creep can also be calculated.
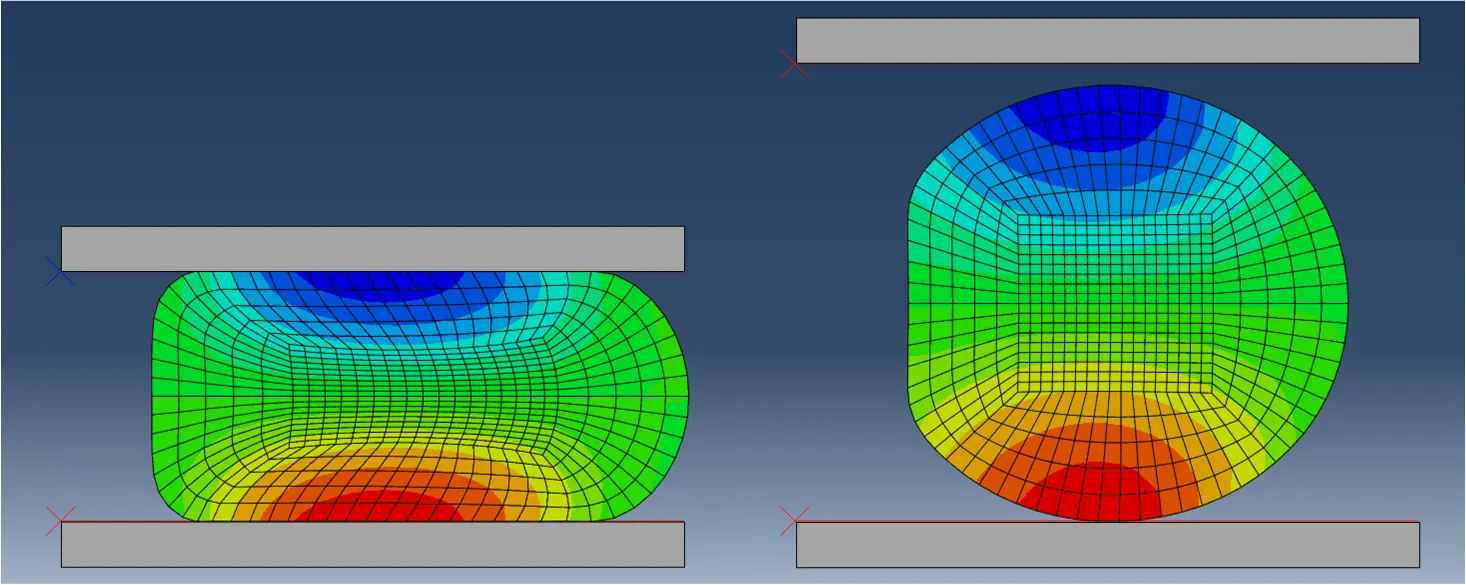
To validate the material models, the tests carried out on the finished components were matched with the corresponding FE simulations. The figure above shows the simulation of the permanent set on the complete roller spring. Here, the spring was compressed with a constant displacement for a period of seven days (Fig. left) in order to determine the permanent deformation afterwards (Fig. right).
The force-displacement curves from the component tests could also be successfully mapped with the simulations.
IMES laboratory infrastructure for measuring high-performance polymers:
At a glance
Participating institutes and centers: Institute of Mechanical Systems IMES
Project Partner: rubber processing industry
Financial contribution: Services and aF&E projects
Project status: ongoing