Machbarkeitsstudie einer AM-gefertigten Spiraldruckfeder
Die Schraubendruckfeder mit zylindrischem Drahtquerschnitt und zylindrischer Wicklungsform ist weit verbreitet und wohl einer der am meisten eingesetzten Federtypen. Es ist schon lange bekannt, dass die Schraubendruckfeder aufgrund ihrer Geometrie eine inhomogene Belastung erfährt, welche dazu führt, dass der Drahtquerschnitt im Regelfall nur zu maximal 50% ausgelastet wird. Dies ergibt sich zwangsläufig aus der Helixform in Verbindung mit einem zylindrischen Drahtquerschnitt, wie er weit verbreitet ist.
Ein Abweichen von einem zylindrischen Drahtquerschnitt ist mit dem bekannten und ansonsten bewährten Wickelprozess zur Herstellung von Schraubendruckfedern nur schwer möglich. Mit den zahlreichen Möglichkeiten des additiven Fertigungsverfahrens Selective Laser Melting (SLM) ergeben sich neue Freiheiten, Bauteile anforderungsgerecht zu gestalten und anschliessend herzustellen.
Es konnte gezeigt werden, dass durch die Parallelschaltung von dünnwandigen und zur Herstellung modifizierten Querschnitten eine Feder mit der gleichen Steifigkeit und dem gleichen Federweg wie bei einer konventionellen Druckfeder aber mit wesentlich reduzierter Masse erzielt werden kann. Für das ausgearbeitete Beispiel wurde eine Gewichtsersparnis von 53% bei gleicher Federsteifigkeit und bei gleichem Federweg und Federlänge erzielt! Die Überprüfung der mechanischen Eigenschaften erfolgte im FE-Programm ANSYS. Die allgemeine Gültigkeit der Methode wurde im untersuchten Bereich nachgewiesen und die bereichsabhängigen Federeigenschaften erläutert.
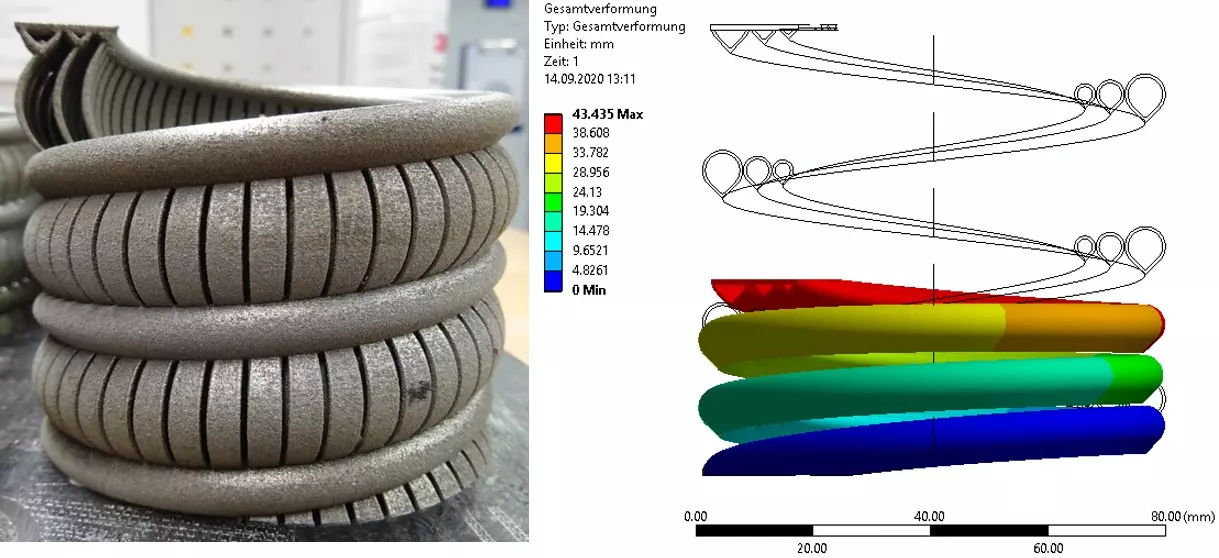
Es wurden zwei Ansätze für den minimalen Einsatz von Stützstrukturen entwickelt und getestet. Die optimierte Federe wurde mithilfe des SLM-Prozesses erfolgreich hergestellt. Das Entfernen der Stützstruktur wurden zu Optimierungszwecken in ANSYS berechnet. Eine Kostenkalkulation für die Prototypen und Serienfertigung von SLM-gefertigten optimierten Druckfedern wurde implementiert. Die Herstellkosten der untersuchten Feder übersteigen gemäss der Berechnung diese der konventionell hergestellten Feder um 8800% für die Losgrösse 1. Für die serielle Herstellung verschlechtert sich das Kostenverhältnis sogar noch. Es konnte gezeigt werden, dass die mit dem Algorithmus in MATLAB ausgelegten Federn in der Nachrechnung mit ANSYS eine gute Übereinstimmung mit den geforderten Federeigenschaften erzielen. Die Herausforderung in der Auslegung besteht darin, die geometrischen Verhältnisse der Querschnitte so zu wählen, dass die Einzelquerschnitte möglichst homogen beansprucht werden und gleichzeitig möglichst wenig Material verwendet wird und der gewünschte Federweg und Federsteifigkeit eingehalten werden.
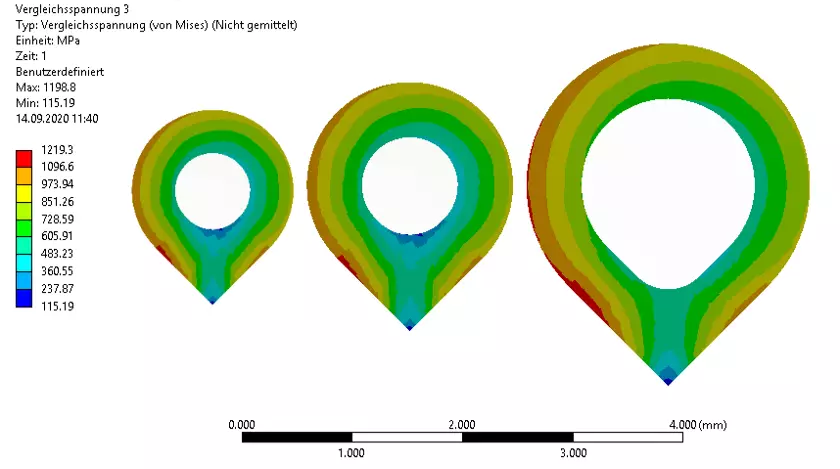
Der Entwicklungsprozess einer gewichtsoptimierten SLM-Feder verkürzt sich mithilfe des Algorithmus drastisch. Durch den entwickelten Optimierungsalgorithmus ist die Wiederholbarkeit von Optimierungsresultaten gewährleistet. Abbildung 3 zeigt eine Designstudie, in welcher für Federn mit unterschiedlicher Steifigkeit und Federweg die Eigenschaften berechnet wurden. Wie daraus zu lesen ist, wird durch den vorgestellten Ansatz (rote Punkte) in jedem Fall eine leichtere Feder als mit einem konventionellen (blaue Punkte) Wickelprozess erzeugt. Jedoch kann je nach Steifigkeit und Federweg eine etwas längere Feder resultieren.
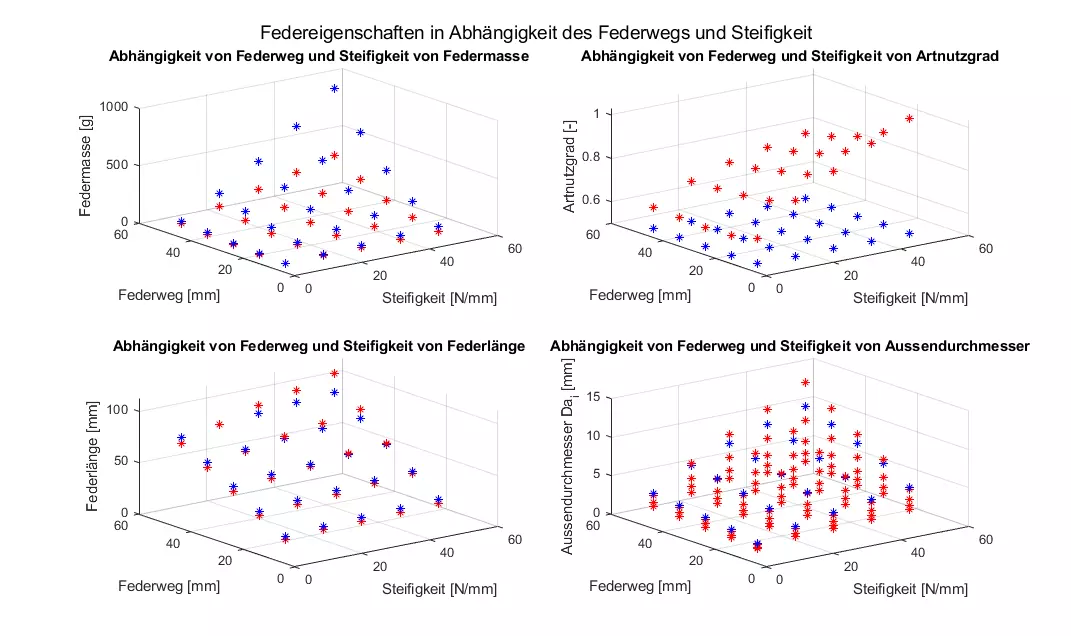
Weiter ermöglicht es automatisierte Auswertungen, um beispielsweise kommerziell interessante Bereiche für SLM-Federn zu ermitteln. Denkbar ist zum Beispiel die Kopplung der Kostenberechnung mit dem Feder-Optimierungsalgorithmus.
Über den Verfasser der Arbeit
Die Machbarkeitsstudie «AM-gefertigten Spiraldruckfeder» wurde von Sandro Mares im Rahmen seines Masterstudiums in Engineering (MSE) erstellt. Betreut wurde er am Institute of Product Development and Production Technologies (IPP) im Schwerpunkt Additive Manufacturing.
Betreuer: Dr. Hans-Jörg Dennig