Simulation of the Pumping Mechanism of Peristaltic Pumps
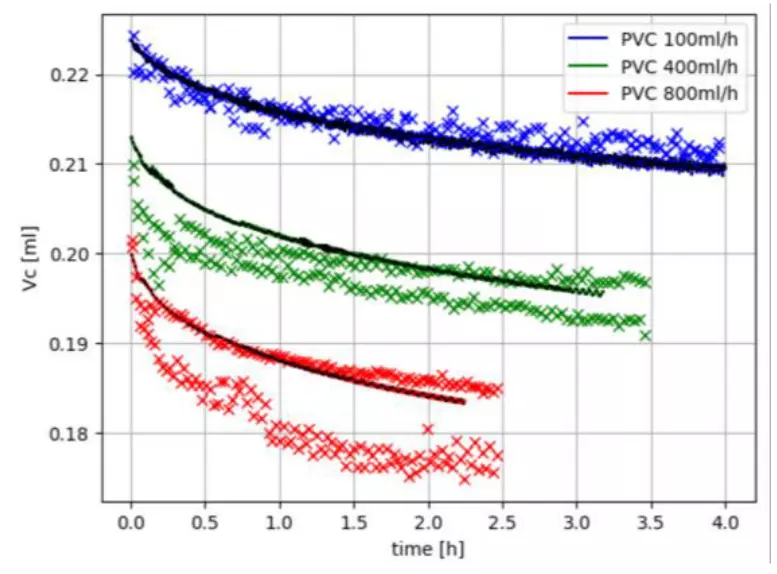
Peristaltic pumps are used for pumping liquids at low flow rates. One of their advantages over other pump types is that the flow rate can be adjusted in proportion to the pump speed and independently of the operating conditions. However, this requires that the mechanical effects of the tube are negligible. Nevertheless, at higher pumping rates or the application-related use of suboptimal tube materials, these effects can significantly impair the delivery volume and have to be considered. As part of an Innosuisse project, a simulation model has been developed to determine the pump characteristics in consideration of the dynamic properties of the tube material.
A large number of different pump types are available for pumping liquids. Each pump principle has its own advantages and disadvantages. Since the selection of a pump system is often limited by the specific application, the weaknesses and limitations of the pump used must be taken into account. Peristaltic pumps, for example, are used where the pumped medium must not come into contact with the environment. They are based on the following principle: The medium, guided in a tube, is conveyed along the tube by specific, mechanical squeezing of the tube’s shape. This is done by means of external rollers or slides, which perform a cyclic movement sequence. Theoretically, the volume conveyed per cycle is constant, since it is determined by the geometry of the external peristaltic. However, this requires that the tube follows this motion consistently and that there is no lift-off of the peristaltic. However, depending on the material properties and conveying speed, lift-off can occur and lead directly to a reduction in throughput.
The prediction of such flow losses requires an understanding of the complex dynamic properties of the tube material under the influence of external boundary conditions such as pumping rate and internal tube pressure. In addition, the mechanical properties of the tube material are subject to temperature and fatigue effects. Until now, the characterization of the pump's characteristics has therefore been determined purely experimentally from a large number of time-consuming measurements. Within the framework of this project, a physical model has now been created to represent the complex viscoelastic material effects and to reproduce the pumping process of a specific peristaltic pump by means of numerical simulation. This enables a much more cost-effective characterization of the pumping system.
Based on the findings of elaborate 3D fluid-structure interaction simulations, the analysis of constitutive material models, and the inclusion of analytical fluid dynamics, a simplified pump model has been developed. It describes the mechanical behavior of the tube inside the peristaltic pump and calculates the resulting flow. In addition, specific measurement methods were developed to determine the relevant tube material properties. For the validation of the results, comparisons with flow measurements on real peristaltic pumps were used.